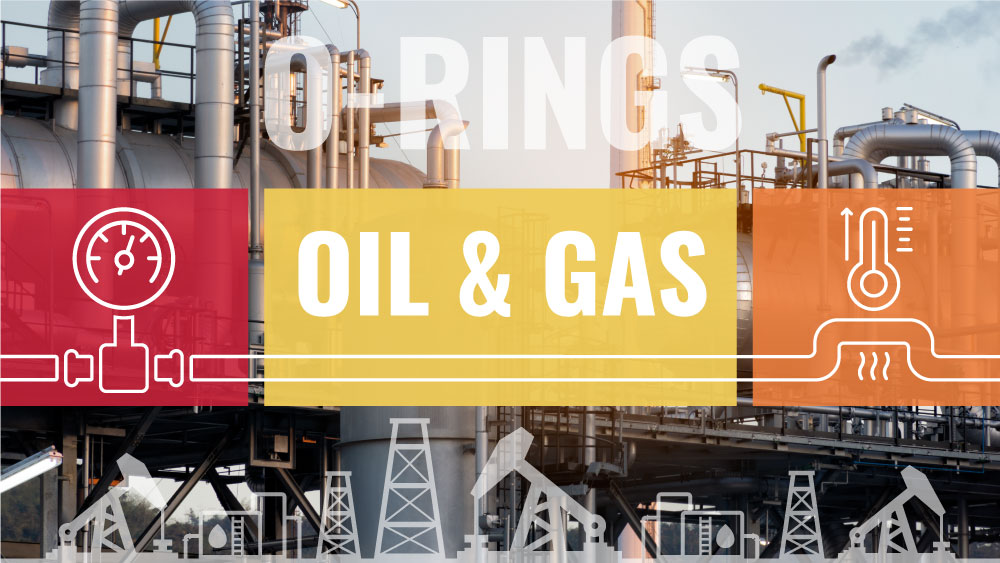
Summary
- O-Rings and seals play crucial roles in the oil and gas industry, from ensuring safety and efficiency to enhancing equipment durability and environmental protection.
- The quality and suitability of o-rings and seals directly influence operational efficiency in the industry, reducing maintenance needs, extending equipment lifespan, and aiding environmental compliance.
- Different materials and types of seals cater to specific demands within the industry, with advancements in material science and technology paving the way for high-performance sealing solutions.
Introduction
In the complex oil and gas industry ecosystem, each component, regardless of size, is pivotal in ensuring seamless operations. The industry, known for its intricate operations involving high pressure and high temperatures, demands reliability, efficiency, and safety in every part of the process. O-Rings and seals maintain operational efficiency, safety, and sustainability in oil and gas processes.
The oil and gas industry comprises various stages – exploration, drilling, production, transportation, and refining. Each step involves numerous pieces of equipment functioning under intense conditions. In all these stages, o-rings and seals are guardians preventing leaks and ensuring system integrity. They may seem insignificant compared to massive drills, pipelines, or refineries. However, if these components do not provide effective sealing, they can compromise the operational efficiency and safety of these large pieces of equipment. Therefore, a comprehensive understanding of the critical role played by o-rings and seals is essential to grasp the nuances of the oil and gas industry.
O-Ring and Seal Functions in the Oil & Gas Sector
O-Rings and seals serve multiple functions in various oil and gas applications. Apart from ensuring safety and enhancing efficiency, they contribute to equipment durability, performance consistency, and environmental protection.
- Safety: In an industry dealing with flammable and hazardous materials, seals and o-rings prevent leaks, which can lead to accidents. They are the first line of defense against potential operational disasters.
- Efficiency: By providing airtight sealing, o-rings and seals ensure the smooth functioning of machinery, reducing energy waste and contributing to overall operational efficiency.
- Durability: High-quality seals and o-rings withstand harsh conditions, extending the lifespan of the equipment that utilizes them.
- Performance Consistency: By preventing leakage and contamination, seals and o-rings help maintain the performance consistency of machinery, which is crucial for quality control in production processes.
- Environmental Protection: Seals and o-rings also play a vital role in preventing the release of gases or fluids into the environment, contributing to environmental protection.
The Importance of Material Selection for O-Rings and Seals
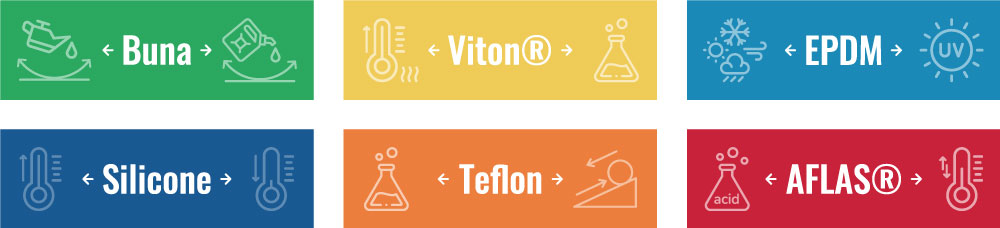
Due to the extreme operational conditions, selecting a suitable material for o-rings and seals is vital for the oil and gas industry. Different materials for o-rings and seals offer unique properties, making them ideal for specific applications within the oil and gas industry.
- Buna (Nitrile): Excellent resistance to oils and fuels makes buna ideal for applications such as oil rig seals, fuel transport pipe seals, and within pumps or valves handling crude oil, diesel fuels, or lubricants.
- Viton® (FKM): Viton®’s superior heat and chemical resistance is advantageous in high-temperature operations like deep drilling, high-pressure valves, and specific refining processes that expose the seals to aggressive chemicals and high temperatures.
- EPDM: The extreme resistance to weather, ozone, and UV rays of EPDM seals makes them perfect for outdoor operations and applications involving steam, like steam lines, outdoor machinery, and heat exchangers.
- Silicone: Its resistance to extreme temperatures makes silicone valuable in environments with broad temperature ranges, such as within wellhead and downhole applications, outdoor machinery exposed to harsh weather, and cryogenic applications.
- Teflon (PTFE): Teflon’s low friction and high resistance to chemicals and temperature make it ideal for aggressive chemical handling equipment, high-speed rotating equipment in fracking operations, and heat exchangers in refining processes.
- AFLAS®: Its excellent heat and chemical resistance, especially to acids, bases, and steam, makes AFLAS® ideal for applications in oil recovery and refining processes involving acidic or basic solutions and steam.
The Role of Special Seals in the Oil & Gas Industry
The proper sealing solution can considerably impact safety, operational efficiency, and overall project success in a highly specialized and demanding industry such as oil and gas. Here’s a look at several types of special seals, their features, and how they fit into the industry:
Viton ETP O-Rings: Viton ETP (Extreme Temperature and Performance) o-rings withstand rapid gas decompression, aggressive chemicals, and extreme temperatures, ideal for high-pressure, high-temperature (HPHT) environments, such as deep-water drilling and specific refining processes.
Rapid Gas Decompression O-Rings: RGD o-rings have a specific design to prevent catastrophic failure caused by rapid pressure changes. They are crucial in applications like wellhead pressure control systems and deep-sea drilling equipment.
High-Visibility O-Rings: The bright color of these components makes them easier to inspect and locate, reducing the risk of installation errors or missing seals. They can be beneficial in any application but are especially useful in complex assembly operations, such as assembling downhole tools or complex pipeline valve systems.
Square Rings: Square Rings provide more sealing surface and better resistance to compression set than standard o-rings. They are helpful in static applications requiring high sealing efficiency, such as flange or hatch seals.
X-Rings: X-Rings offer two sealing surfaces and resist spiral twists, making them ideal for dynamic rotary applications, such as rotating shafts or pump impellers in drilling or fluid handling equipment.
Backup Rings: These rings prevent o-ring extrusion in high-pressure applications, adding to the seal’s lifespan. They are often in high-pressure valves, BOPs, or hydraulic systems in drilling rigs.
Oil Seals: Oil Seals are used to seal around rotating shafts and prevent the leakage of lubricants. They find use in rotary equipment like pumps, compressors, and gearboxes in various oil and gas operations.
Loaded U-Cups: Loaded U-Cups provide excellent sealing efficiency and are resistant to wear and extrusion, making them suitable for static and dynamic hydraulic applications like hydraulic cylinders in drilling equipment.
End Caps: End Caps are used to protect the seal and bearing areas in rotary shaft applications, helpful in rotating equipment like motors and pumps in oil and gas operations.
V-Rings: V-Rings are used as secondary seals to protect primary seals from dirt, dust, and grease. They are often in dusty or muddy environments like oil field machinery or offshore drilling equipment.
Gamma Seals: The design of these seals allows them to resist degradation from gamma radiation, perfect for nuclear-enhanced oil recovery operations or operations dealing with naturally occurring radioactive materials (NORMs).
The Impact of O-Rings and Seals on Operational Efficiency
The quality and appropriateness of seals and o-rings directly impact the efficiency of oil and gas operations in several ways:
- Reduced Maintenance: High-quality seals minimize leakage and seal failures, reducing maintenance requirements and downtime.
- Enhanced Equipment Lifespan: By providing effective sealing under extreme conditions, quality seals extend the lifespan of equipment, saving replacement costs.
- Improved Safety: Effective seals reduce the risk of leaks of hazardous materials, contributing to safer operations.
- Environmental Compliance: Good sealing prevents the escape of harmful substances into the environment, aiding in compliance with environmental regulations.
Case Study: Elastomer Seal Failure in Deepwater Horizon Disaster
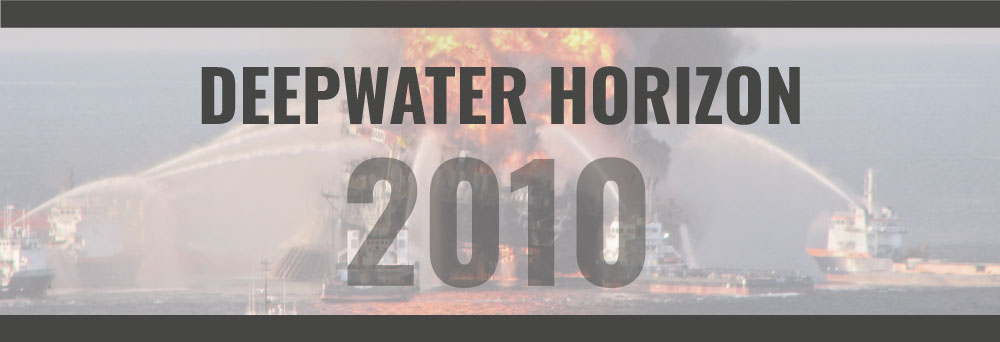
The Deepwater Horizon oil spill in the Gulf of Mexico in 2010 was one of history’s most catastrophic environmental disasters. The blowout resulted in the loss of 11 lives and spilled approximately 4.9 million barrels of oil into the ocean over 87 days.
The incident began with a well integrity failure, followed by a loss of control over the well. The blowout preventer (BOP), a safety device designed to shut off the well in emergencies, failed to activate properly. Investigations after the incident found that the BOP’s blind shear ram – a device meant to cut through the drill pipe and seal the well – had failed to close fully. A key contributing factor to this failure was the poor performance of the elastomer seals within the BOP.
The elastomer seals could not effectively seal the well when the pipe was off-center, which was the situation at the time of the accident. Reports indicated that the elastomer material could not effectively withstand the harsh environment, including the extreme pressures and temperatures at the well’s depth.
As a result of this disaster and the subsequent investigation, industry standards have been revised and enhanced. There is now a much greater focus on testing and verifying the performance of elastomer seals and other BOP components under realistic operating conditions such as extreme temperatures, pressures, and aggressive chemical environments. As a result, new materials, like the last generation of FFKM (Perfluroelastomer) compounds, gained prominence due to their better performance in extreme conditions. The incident underscored the critical role of o-rings and seals in maintaining safety and operational integrity in the oil and gas industry.
The Future of Sealing Solutions in Oil & Gas
The oil and gas industry is continually evolving, and sealing solutions must keep up. Advances in material science are leading to more durable, resilient, and efficient seals and o-rings. For instance, the development of FFKM provides seals with almost the same chemical resistance as PTFE while offering the elasticity of elastomers.
Similarly, the shift towards unconventional resources, deep-sea drilling, and high-pressure high-temperature (HPHT) applications demands innovative sealing solutions. Seals for these applications need to withstand extreme conditions while providing reliable performance.
Furthermore, digital transformation is impacting the future of sealing solutions. Digital technologies enable predictive maintenance, where seal wear can be detected early using sensors and data analytics, allowing for timely replacement and reduced downtime.
The Role of Technology in Advancing O-Ring and Seal Performance
Technology plays a vital role in enhancing seal performance. Advanced manufacturing techniques allow for the precise production of seals with minimal errors. For instance, CNC machines can produce seals with tight tolerances, ensuring a perfect fit for each application.
Moreover, materials technology is enabling the creation of seals with superior properties. For example, researchers utilize nanotechnology to enhance seals’ mechanical strength and wear resistance.
Predictive maintenance utilizes technologies like machine learning and data analytics. By analyzing sensor data, these technologies can predict seal failures before they occur, enabling timely replacements and minimizing downtime.
Conclusion
The role of o-rings and seals in the oil and gas industry is undeniable. They ensure operational safety, contribute to efficiency, and are increasingly central to sustainability efforts. The demand for innovative, high-performance sealing solutions grows as the industry continues to evolve.
At this juncture, partnering with a knowledgeable and experienced provider becomes crucial. Global O-Ring and Seal, as a master distributor of o-rings, backup rings, x-rings, cord stock, and related seals, has the expertise to guide you through the complexities of seal selection, ensuring you get the most suitable and efficient solutions. Global O-Ring and Seal can meet the ever-evolving demands of the oil and gas industry with a wide range of AS568 standard sizes, metric sizes, and o-ring cord stock.