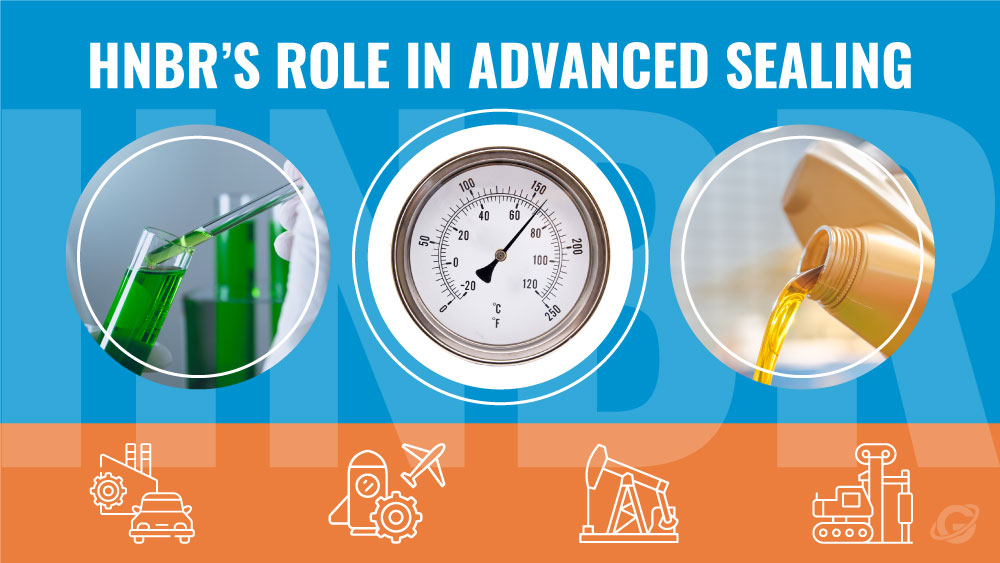
Resumen
- El caucho de nitrilo butadieno hidrogenado (HNBR) es un material fundamental en las industrias, ya que ofrece una resistencia superior a las altas temperaturas, aceites y productos químicos, lo que mejora la seguridad y la eficiencia operativa.
- Las propiedades únicas del HNBR incluyen una excelente estabilidad térmica, resistencia al aceite y a los productos químicos, y resistencia mecánica, lo que lo hace ideal para aplicaciones exigentes de automoción, aeroespacial, petróleo y gas y maquinaria pesada.
- A pesar de su solidez, comprender las limitaciones y la aplicación adecuada del HNBR es crucial para un rendimiento óptimo, lo que garantiza la longevidad y la confiabilidad en diversos entornos industriales.
Introducción
En el mundo dinámico y en constante evolución de las aplicaciones industriales, la búsqueda de materiales que combinen durabilidad, resistencia y versatilidad ha dado lugar a importantes avances científicos. Uno de esos avances es el desarrollo del caucho de nitrilo butadieno hidrogenado (HNBR), un material que ha revolucionado la forma en que las industrias abordan el sellado y la longevidad en entornos hostiles. Esta publicación de blog explora el fascinante mundo del HNBR, sus inicios, las características del material, las aplicaciones en entornos de alta temperatura y su papel indispensable en el campo.
Descripción general de las juntas tóricas HNBR

El caucho de nitrilo butadieno hidrogenado (HNBR) , un avance significativo con respecto a su predecesor , el caucho de nitrilo butadieno (NBR) , es un testimonio de los avances logrados en la ciencia de los materiales en las últimas décadas. Una búsqueda en toda la industria de materiales que pudieran soportar entornos más exigentes, específicamente aquellos con temperaturas extremas, aceites y productos químicos, dio como resultado el nacimiento de HNBR. HNBR surgió como un elastómero robusto y versátil caracterizado por su estructura molecular mejorada que ofrece resistencia y resistencia mecánica superiores. A medida que las industrias continúan evolucionando y enfrentan nuevos desafíos, es probable que el papel de HNBR se expanda, impulsado por su trayectoria comprobada y sus mejoras continuas.
Las mejoras continuas y los avances tecnológicos marcaron el recorrido histórico de las juntas tóricas HNBR. Originario de NBR, HNBR fue desarrollado para abordar las limitaciones que enfrentaba su predecesor, particularmente en términos de resistencia a la temperatura y longevidad. Si bien es útil en diversas aplicaciones, el NBR tuvo problemas en condiciones extremas, lo que llevó a los investigadores a buscar un material más resistente. El gran avance se produjo con el proceso de hidrogenación, en el que los enlaces insaturados de los segmentos de butadieno del NBR se hidrogenaron selectivamente, mejorando significativamente la estabilidad térmica y la resistencia del material. Este proceso marcó un punto de inflexión, dando como resultado un caucho que podía soportar condiciones mucho más duras.
A lo largo de los años, se han realizado avances continuos en la formulación y procesamiento de HNBR, mejorando sus propiedades y ampliando su aplicabilidad. Estos desarrollos fueron una respuesta a las exigentes condiciones de las industrias petrolera y automotriz y a las necesidades anticipadas de tecnologías y sectores emergentes. Mejorar la capacidad de resistir el ozono, la oxidación y diversos productos químicos y ampliar el rango de temperatura fue fundamental para la transición del HNBR de una solución especializada a una opción principal para numerosas aplicaciones.
La adopción de HNBR es más notable en sectores donde la confiabilidad y el desempeño bajo estrés no son negociables. En la industria automotriz, es un material de elección para soluciones de sellado con motores, transmisiones y sistemas de combustible, donde debe soportar temperaturas fluctuantes y exposición a aceites y combustibles. De manera similar, la resistencia del HNBR a productos químicos agresivos y condiciones extremas lo hace indispensable para sellar componentes en equipos de perforación y tuberías en el sector del petróleo y el gas. Más allá de estos, su presencia también es importante en el sector aeroespacial, manufacturero y farmacéutico, entre otros campos, donde sus propiedades únicas garantizan seguridad y eficiencia.
Las ventajas de utilizar HNBR en aplicaciones industriales son claras e impactantes. Su excepcional durabilidad a altas temperaturas y en presencia de aceites y productos químicos reduce la necesidad de reemplazos y mantenimiento frecuentes, garantizando continuidad operativa y seguridad. Las robustas propiedades mecánicas del material, incluida una excelente resistencia a la tracción y al desgarro, lo hacen adecuado para diversas aplicaciones dinámicas y estáticas. Además, los beneficios económicos del HNBR, debido a su longevidad y menores necesidades de mantenimiento, lo convierten en una solución rentable para muchas industrias.
Características de las juntas tóricas HNBR
HNBR es un material elogiado por sus propiedades excepcionales, lo que lo hace adecuado para diversas aplicaciones exigentes. Las características distintivas del HNBR están intrínsecamente ligadas a su composición química única, lo que explica su rendimiento superior en diversas condiciones. Comprender los atributos del material de HNBR proporciona información sobre su versatilidad e idoneidad para aplicaciones industriales desafiantes.
HNBR es una versión hidrogenada de NBR. El proceso de hidrogenación reduce significativamente la cantidad de dobles enlaces en el componente butadieno del NBR, lo que da como resultado una estructura principal saturada. Esta saturación es crucial, ya que confiere al HNBR propiedades mejoradas de estabilidad y resistencia. El grado de hidrogenación afecta directamente las propiedades del material; niveles más altos suelen producir una mejor resistencia al calor y a los productos químicos.
La columna vertebral hidrogenada del HNBR proporciona una notable estabilidad térmica y resistencia al calor. A diferencia de muchos otros cauchos, el HNBR puede soportar una exposición prolongada a temperaturas que van desde -40 °F (-40 °C) a +302 °F (+150 °C) e incluso más durante períodos cortos, dependiendo de la formulación, lo que lo convierte en un Excelente material para aplicaciones que involucran fluidos y gases a alta temperatura. La estabilidad a temperaturas elevadas es crucial para prevenir la degradación, mantener la integridad del sello y garantizar la longevidad de los componentes.
La naturaleza saturada de la estructura del HNBR mejora su resistencia a aceites, combustibles y diversos productos químicos. A diferencia de los cauchos insaturados, la falta de dobles enlaces impide que el material reaccione o se degrade fácilmente con sustancias agresivas. La resistencia es particularmente beneficiosa en las industrias automotriz y de petróleo y gas, donde los sellos y componentes deben soportar la exposición a fluidos agresivos sin hincharse, agrietarse o degradarse, lo que garantiza un rendimiento confiable y seguridad.
El HNBR exhibe excelentes propiedades mecánicas, incluida una alta resistencia a la tracción y al desgarro debido a la saturación de su cadena de polímero y el potencial de reticulación dentro del material. Los fuertes enlaces covalentes y la estructura uniforme resisten las tensiones físicas, lo que hace que el HNBR sea ideal para aplicaciones dinámicas donde los componentes probablemente experimentarán estiramiento, compresión y otras fuerzas. La capacidad del material para mantener su integridad bajo tensión contribuye a la durabilidad y confiabilidad de los sellos y componentes fabricados con HNBR.
HNBR mantiene una deformación por compresión baja, lo que significa que puede volver a su forma original después de ser comprimido, lo cual es fundamental para mantener un sello eficaz a lo largo del tiempo. La elasticidad del material es esencial en aplicaciones donde los sellos deben adaptarse repetidamente a presiones y temperaturas variables sin perder su capacidad de sellado. Esta resiliencia ayuda a prevenir fugas, minimiza los requisitos de mantenimiento y extiende la vida útil de los componentes.
La combinación de estabilidad térmica, resistencia química y resistencia mecánica hace que el HNBR sea excepcionalmente duradero y duradero, incluso en entornos industriales hostiles. Resiste la degradación por factores externos como el ozono, la luz solar y condiciones climáticas extremas, manteniendo su rendimiento en el tiempo. Esta longevidad es fundamental para reducir la necesidad de reemplazos frecuentes, reducir los costos operativos y minimizar el tiempo de inactividad en aplicaciones críticas.
Si bien el HNBR es un material versátil y robusto, es esencial reconocer sus limitaciones. Por ejemplo, es posible que no funcione tan bien en temperaturas extremadamente bajas en comparación con algunos materiales especializados. Además, ciertas condiciones y químicos agresivos aún pueden afectar el HNBR, especialmente si no se formulan correctamente para el entorno específico. Por lo tanto, comprender los requisitos de aplicación específicos y las posibles condiciones de exposición es crucial al seleccionar HNBR para un uso particular.
Aplicaciones de alta temperatura de juntas tóricas HNBR
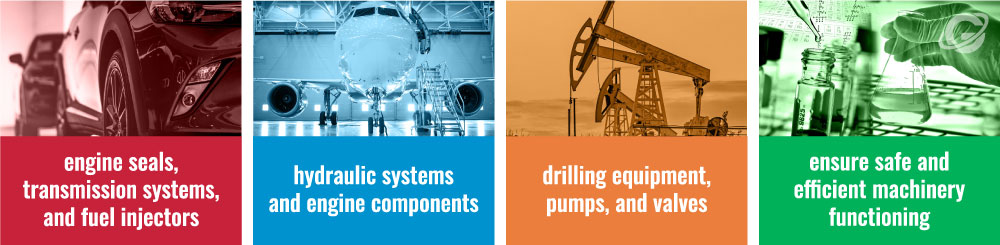
Las juntas tóricas de HNBR se han convertido en una piedra angular en industrias donde prevalecen las aplicaciones de alta temperatura. Sus propiedades únicas los hacen indispensables para mantener la integridad del sistema y garantizar operaciones seguras y eficientes. Comprender cómo funcionan las juntas tóricas de HNBR en estas condiciones extremas proporciona información sobre su papel fundamental en diversos sectores industriales.
Las aplicaciones de alta temperatura están muy extendidas en numerosas industrias, incluidas la automovilística, la aeroespacial, la de petróleo y gas y la manufacturera. En el sector automotriz , las juntas tóricas de HNBR son esenciales para los sellos de motores, sistemas de transmisión e inyectores de combustible, donde enfrentan altas temperaturas y fluidos agresivos. La industria aeroespacial confía en ellos para sistemas hidráulicos y componentes de motores que deben funcionar de manera confiable a temperaturas elevadas. De manera similar, los equipos de perforación, bombas y válvulas en operaciones de petróleo y gas utilizan juntas tóricas de HNBR, donde es probable que el sello esté expuesto a altas tensiones térmicas y químicas. En los procesos de fabricación , como la producción química y la generación de energía, estas juntas tóricas garantizan el funcionamiento seguro y eficiente de la maquinaria y los sistemas de contención.
Las juntas tóricas de HNBR son fundamentales para mantener la integridad de los sistemas que funcionan a altas temperaturas. Proporcionan sellos confiables que previenen fugas, resisten la degradación y mantienen sus propiedades elásticas incluso cuando se exponen a calor prolongado. La capacidad de las juntas tóricas de HNBR para soportar condiciones adversas manteniendo su forma y funcionalidad es crucial para prevenir fallas del sistema, minimizar el tiempo de inactividad y garantizar un funcionamiento continuo. Su desempeño impacta directamente en la seguridad, eficiencia y longevidad de los equipos y procesos de los que forman parte.
Las altas temperaturas pueden afectar significativamente el rendimiento de los materiales de sellado. La exposición prolongada puede provocar endurecimiento, pérdida de elasticidad e incluso degradación, comprometiendo el sellado y provocando fallos. Sin embargo, las juntas tóricas de HNBR contrarrestan estos efectos. Su estabilidad térmica mejorada significa que pueden funcionar eficazmente en temperaturas que oscilan entre -40 °C y 150 °C y, a veces, incluso más altas durante períodos cortos. El proceso de hidrogenación al que se somete el HNBR aumenta su resistencia a la degradación térmica, lo que le permite mantener sus propiedades mecánicas y capacidades de sellado incluso bajo calor extremo.
En operaciones a alta temperatura, la seguridad tanto del personal como del equipo es primordial. Una falla en un componente de sellado puede provocar fugas, derrames o averías del sistema, lo que supone riesgos para la seguridad y el medio ambiente. Las juntas tóricas de HNBR contribuyen significativamente a la seguridad operativa al proporcionar sellos confiables que resisten condiciones extremas sin fallar. Su uso ayuda a prevenir accidentes y mal funcionamiento, garantizando que los sistemas funcionen dentro de parámetros seguros. Sin embargo, también es fundamental inspeccionar y mantener periódicamente estos componentes, ya que incluso los materiales más robustos pueden eventualmente sucumbir a las tensiones de los entornos hostiles.
Juntas tóricas de HNBR en el campo
Debido a sus robustas propiedades y versatilidad, las juntas tóricas de HNBR se han vuelto cruciales en diversas aplicaciones de campo. Su desempeño en entornos del mundo real ilustra su importancia y resalta los desafíos y consideraciones asociados con su uso. Comprender estos aspectos garantiza que el HNBR siga siendo el material elegido por quienes buscan soluciones de sellado confiables y sostenibles.
Varias aplicaciones que requieren un rendimiento superior en condiciones adversas utilizan juntas tóricas de HNBR. En los sistemas HVAC, las juntas tóricas HNBR garantizan la eficiencia y la longevidad de las unidades de calefacción, ventilación y aire acondicionado, especialmente aquellas que operan en entornos de alta temperatura o manipulan refrigerantes. Las juntas tóricas de estos sistemas deben resistir la hinchazón y la degradación causadas por la exposición a varios gases y productos químicos. Las juntas tóricas de HNBR son esenciales para sistemas hidráulicos, motores y otros componentes sujetos a altas tensiones, materiales abrasivos y temperaturas fluctuantes en maquinaria pesada. Ayudan a mantener la integridad y el rendimiento de los equipos de construcción, minería y agricultura. Cada una de estas aplicaciones aprovecha las propiedades únicas de HNBR para garantizar la confiabilidad y seguridad en las operaciones.
Los beneficios reales de las juntas tóricas de HNBR son numerosos. Su excelente resistencia al calor y a los productos químicos los hace ideales para entornos hostiles donde otros materiales fallarían. Esta confiabilidad asegura la longevidad de los sistemas que lo componen, reduciendo el tiempo de inactividad y los costos de mantenimiento. Además, su resistencia mecánica y resistencia a la abrasión y al desgarro significa que pueden soportar tensiones físicas y seguir proporcionando un sellado fiable. Esta resiliencia es particularmente beneficiosa en aplicaciones dinámicas donde las juntas tóricas están sujetas a movimientos constantes y cambios de presión.
A pesar de su robustez, las juntas tóricas de HNBR presentan desafíos. La exposición a condiciones extremas puede eventualmente provocar degradación, y una instalación o selección inadecuada puede provocar fallas prematuras. Es fundamental comprender las demandas específicas de la aplicación y elegir el grado y la formulación adecuados de HNBR para superar estos desafíos. La inspección y el mantenimiento periódicos son vitales para identificar y abordar problemas potenciales antes de que provoquen fallas. Al mantenerse informados sobre los últimos avances y mejores prácticas, los profesionales pueden garantizar el rendimiento óptimo de las juntas tóricas HNBR en el campo.
A medida que las industrias se centran cada vez más en la sostenibilidad y la reducción del impacto ambiental, materiales como el HNBR se vuelven aún más críticos. Las juntas tóricas de HNBR contribuyen a la sostenibilidad ambiental al mejorar la eficiencia y la longevidad de los sistemas, lo que lleva a una reducción de desechos y menos recursos consumidos con el tiempo. Sin embargo, también es esencial considerar todo el ciclo de vida del producto, desde la producción hasta la eliminación. Se están realizando esfuerzos para hacer que la producción de HNBR sea más respetuosa con el medio ambiente y para desarrollar métodos de reciclaje y eliminación que minimicen su impacto en el medio ambiente.
Conclusión
El viaje de HNBR desde una innovación científica hasta una piedra angular en numerosas industrias subraya la importancia de la ciencia de los materiales para promover la eficiencia, la seguridad y la sostenibilidad industriales. A medida que las industrias sigan evolucionando y afrontando nuevos desafíos, el papel de materiales como el HNBR será cada vez más significativo y seguirá dando forma al futuro de la tecnología y las aplicaciones industriales. Al comprender y aprovechar las fortalezas de HNBR, las industrias pueden garantizar un futuro en el que el rendimiento y la durabilidad vayan de la mano con el progreso y la innovación.