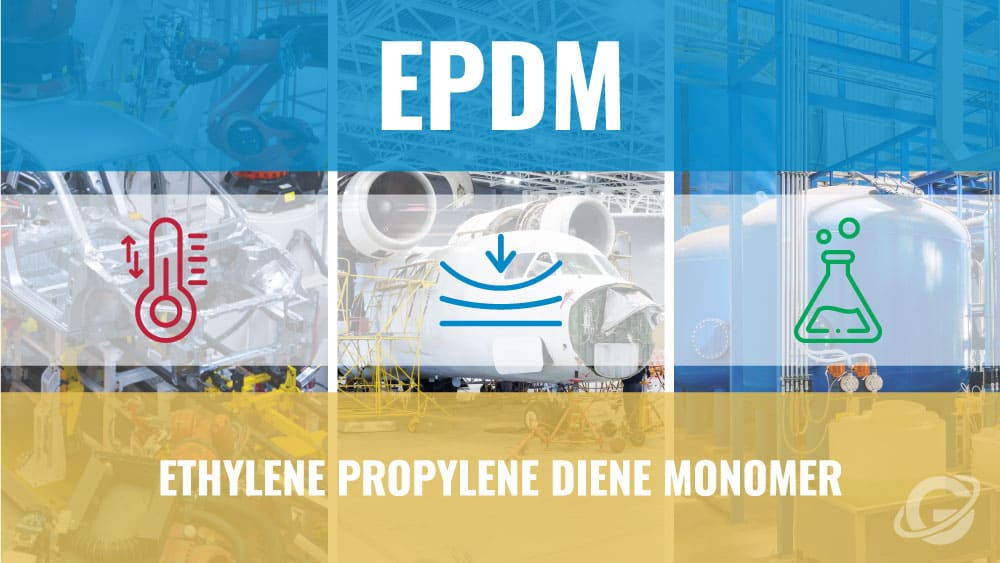
Résumé
- Les joints EPDM sont connus pour leur résistance chimique, leur résilience à la température et leur flexibilité exceptionnelles, ce qui les rend parfaitement adaptés à diverses applications industrielles.
- Dotés d'une rentabilité, d'une longue durée de vie et d'exigences de maintenance minimales, les joints EPDM offrent de solides avantages dans des secteurs tels que l'automobile, l'aérospatiale et le traitement de l'eau.
- Le choix entre l'EPDM durci au peroxyde et au soufre offre des options nuancées pour les besoins d'application spécifiques, impactant en conséquence leurs propriétés mécaniques et chimiques.
Introduction
La sélection de matériaux d'étanchéité appropriés est un facteur essentiel pour optimiser les performances, la longévité et la sécurité dans diverses applications industrielles. L'éthylène propylène diène monomère (EPDM) s'est distingué comme un matériau de choix, offrant une large gamme de caractéristiques et d'avantages adaptés à diverses exigences industrielles. Ce blog analyse de manière approfondie les joints EPDM, élucidant leurs caractéristiques, leurs avantages multiformes et leurs applications courantes. De plus, l'article explorera les variables à prendre en compte lors du choix entre différents types de cures EPDM.
Qu’est-ce que l’EPDM ?
L'éthylène propylène diène monomère, communément appelé EPDM, est un élastomère de caoutchouc synthétique réputé pour résister à plusieurs conditions environnementales. Principalement composé d'éthylène et de propylène, dérivés du pétrole et du gaz naturel, l'EPDM contient également un composant diène qui sert d'agent de réticulation. Cette composition chimique unique confère à l'EPDM une résistance impressionnante à l'ozone, aux substances polaires et à l'eau chaude et froide.
Développé dans les années 1960, l'EPDM est apparu alors que des industries comme l'automobile et l'aéronautique recherchaient des matériaux plus robustes pour résister aux environnements difficiles. Depuis lors, l’EPDM constitue une option fiable pour diverses applications industrielles, grâce à ses propriétés mécaniques exceptionnelles. Notamment, le matériau présente une flexibilité et une durabilité, fonctionnant généralement entre -67°F et 257°F.
Lorsque vous comparez l'EPDM à d'autres matériaux d'étanchéité populaires comme le Buna (Nitrile) et le Viton® (FKM), l'EPDM se distingue par sa résistance supérieure à l'eau et aux intempéries. Buna excelle dans les applications à base d'huile et Viton® est bien adapté aux environnements à haute température. Le seuil en EPDM est exceptionnellement polyvalent, avec la capacité de résister efficacement à l’humidité, à l’ozone et aux rayons UV.
La fabrication de joints EPDM implique souvent le moulage par injection de caoutchouc. Dans ce processus, le matériau EPDM brut est chauffé jusqu'à ce qu'il devienne malléable, puis est injecté dans un moule ayant la forme du joint souhaité. Après refroidissement, le joint est extrait et subit un processus de durcissement pour atteindre ses propriétés finales prêtes à être appliquées.
La durabilité environnementale est un autre domaine dans lequel l’EPDM brille. Le matériau est recyclable et possède une longue durée de vie, ce qui signifie un remplacement moins fréquent et, par conséquent, moins de déchets. De plus, le processus de fabrication de l’EPDM est relativement peu toxique, ce qui renforce encore sa position en tant que choix écologique de caoutchouc synthétique.
Caractéristiques des joints EPDM
Les caractéristiques d’un matériau sont primordiales pour déterminer son adéquation à des applications spécifiques. Parmi la large gamme de matériaux d'étanchéité disponibles, les joints EPDM possèdent un ensemble unique de caractéristiques qui les rendent très polyvalents et efficaces dans divers contextes industriels.
L'EPDM est réputé pour sa résistance chimique exceptionnelle aux acides dilués, aux alcalins et aux solvants polaires comme les cétones et les alcools. Cette fonctionnalité le rend inestimable pour les applications dans le traitement chimique, le traitement des eaux usées et l'industrie pharmaceutique. La résistance chimique de l'EPDM est due à son squelette élastomère saturé, qui offre stabilité et inertie face à de nombreux produits chimiques réactifs. La résistance du matériau à une large gamme de valeurs de pH, allant des acides dilués aux alcalins, est attribuée à sa structure moléculaire polaire qui facilite de fortes forces intermoléculaires, offrant une résistance aux attaques chimiques corrosives.
La résilience à la température est une autre qualité notable des joints EPDM, issue de son architecture polymère unique, qui implique un monomère diène qui permet la réticulation. Cette réticulation contribue à la haute résistance à la traction du matériau et à sa capacité à résister à une large plage de températures, allant des basses cryogéniques de -67°F aux températures élevées de 257°F. Lorsqu'il est utilisé dans des climats glacials ou dans des applications à haute température telles que les systèmes à vapeur, l'EPDM conserve ses propriétés physiques, minimisant ainsi le risque de défaillance du joint dû aux fluctuations thermiques.
Concernant la flexibilité et la durabilité, l'EPDM doit ses performances à sa nature élastomère unique et à un degré élevé d'enchevêtrement polymère. Sa structure amorphe permet une meilleure répartition du volume libre, ce qui se traduit par une flexibilité accrue. L'EPDM présente également une résistance élevée à la fatigue et une faible déformation rémanente à la compression en raison de son architecture moléculaire, qui résiste intrinsèquement à l'abrasion, à la déchirure et aux chocs.
L'EPDM se distingue par sa capacité à résister à une exposition prolongée aux rayons UV, à l'ozone et aux conditions météorologiques extrêmes. Cette caractéristique découle de sa saturation et de la présence d'antioxydants protecteurs et de stabilisants UV qui empêchent la dégradation oxydative. La résistance intrinsèque du matériau aux rayons UV, à l'ozone et à d'autres agents oxydants provient de sa nature apolaire, qui limite la formation de radicaux libres responsables du vieillissement et de la dégradation du matériau. Cette propriété le rend particulièrement utile pour les applications extérieures, comme les machines de construction ou les coupe-froid automobiles, où les joints sont régulièrement exposés aux éléments.
La constante diélectrique et la rigidité diélectrique de l'EPDM en font un excellent isolant électrique. Le matériau a un faible facteur de dissipation et sa structure non polaire minimise le libre mouvement des ions, le rendant ainsi résistant à la conductivité électrique. Cette isolation électrique est particulièrement cruciale dans les applications nécessitant une isolation électrique stricte.
L’un de ces attributs moins discutés mais précieux de l’EPDM est sa stabilité de couleur. En raison de l'absence de doubles liaisons dans sa structure, la résistance du matériau à la dégradation photo-oxydative permet la longévité des couleurs et la capacité de conserver sa teinte d'origine. Lorsqu'il est combiné avec des pigments ou des colorants, le matériau présente d'excellentes propriétés de solidité des couleurs, ce qui le rend idéal pour les applications esthétiquement sensibles où la fidélité des couleurs est essentielle.
Avantages de l'utilisation des joints EPDM
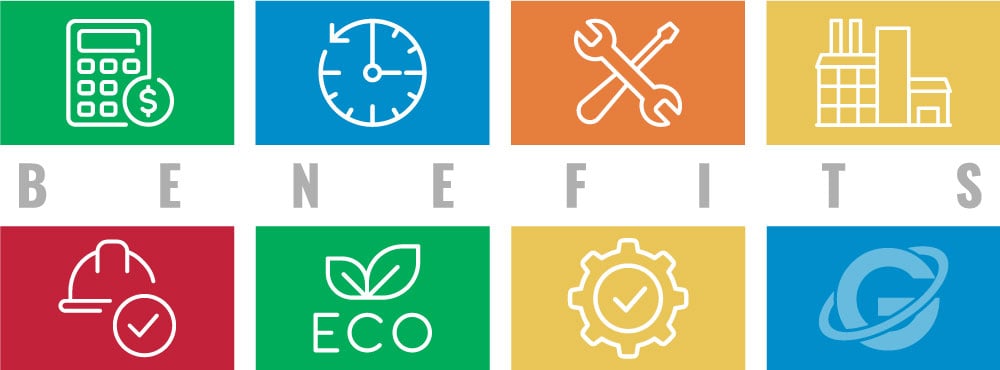
La vaste gamme de fonctionnalités offertes par les joints EPDM se traduit naturellement par divers avantages, ce qui en fait un choix recherché dans de nombreux secteurs. Nous examinons ici les principaux avantages qui distinguent les joints EPDM de leurs homologues.
- Rentabilité : les joints EPDM sont souvent plus rentables que d'autres matériaux d'étanchéité comme le Viton® ou le silicone si l'on considère leur durée de vie et leurs caractéristiques de performance. Leur résistance aux facteurs environnementaux et à un large éventail de produits chimiques réduit le besoin de remplacements fréquents, contribuant ainsi aux économies globales.
- Longévité dans les applications : Grâce à leurs propriétés chimiques et mécaniques robustes, les joints EPDM présentent une longue durée de vie. Leur résistance à la dégradation due à différents facteurs externes garantit leur efficacité sur de longues périodes, réduisant ainsi le coût global de possession.
- Exigences minimales d'entretien : les joints EPDM nécessitent généralement moins d'entretien en raison de leur durabilité et de leur résistance aux conditions environnementales. Cet avantage se traduit par moins de temps d’arrêt des équipements et une réduction des coûts de main-d’œuvre de maintenance.
- Polyvalence dans plusieurs secteurs : Les propriétés chimiques, mécaniques et thermiques des joints EPDM les rendent très polyvalents. Ils trouvent une large application dans des secteurs tels que l’automobile, l’aérospatiale, le traitement de l’eau et l’industrie pharmaceutique.
- Caractéristiques de sécurité améliorées : l'excellente résistance chimique et la stabilité thermique de l'EPDM améliorent la sécurité en minimisant le risque de défaillance du joint pouvant entraîner des fuites ou d'autres conditions dangereuses. Les propriétés isolantes du matériau en font également un choix privilégié dans les applications électriques pour une sécurité accrue.
- Avantages environnementaux : La longue durée de vie et la recyclabilité de l'EPDM contribuent à ses avantages environnementaux. De plus, ses processus de production sont relativement peu toxiques, ce qui en fait une option plus durable que les autres matériaux d'étanchéité.
- Facilité d'installation : les joints EPDM sont plus faciles à installer que les autres types en raison de leur flexibilité et de leurs propriétés élastiques. Ils peuvent souvent être appliqués sans outils ni adhésifs spécialisés, ce qui rend le processus d'installation rapide et simple.
Applications courantes des joints EPDM

L'industrie automobile s'appuie fortement sur la durabilité et la résistance chimique des joints EPDM. Ces qualités sont cruciales dans les applications automobiles, telles que les systèmes de refroidissement, les systèmes de freinage et la climatisation, où les joints sont exposés à de nombreuses températures et à des fluides potentiellement corrosifs. La longévité et les exigences minimales d'entretien des joints EPDM en font un choix privilégié dans la construction automobile, conduisant à des véhicules plus fiables et plus rentables.
Les installations de traitement de l’eau bénéficient également de l’utilisation de joints EPDM. La résistance de l'EPDM aux acides et aux alcalis diluants constitue un avantage significatif dans les applications de traitement de l'eau et des eaux usées. Ici, les phoques sont exposés à des produits chimiques comme le chlore ou d’autres désinfectants. La résistance chimique de l'EPDM garantit l'intégrité des joints, réduisant ainsi le risque de fuite et améliorant la sécurité globale de l'usine.
Dans les industries pharmaceutique et alimentaire, la nature non toxique et conforme à la FDA des joints EPDM les rend idéaux pour une utilisation dans divers équipements de traitement. Ces industries ont souvent des réglementations strictes en matière de sécurité des matériaux et d'hygiène. La stabilité chimique de l’EPDM le rend adapté aux applications impliquant une exposition à des formulations pharmaceutiques ou à des produits chimiques de qualité alimentaire. La longévité des joints garantit également des performances constantes, réduisant ainsi la fréquence de remplacement et les temps d'arrêt potentiels.
Les applications aérospatiales présentent des défis uniques tels que des fluctuations de température extrêmes et la nécessité de matériaux légers mais robustes. Les joints EPDM sont ici avantageux en raison de leur résilience thermique et de leur faible poids. Ils sont courants dans les systèmes hydrauliques, les systèmes de carburant et les applications d’étanchéité des cabines des avions. Les caractéristiques de sécurité améliorées de l'EPDM, notamment la résistance chimique et la stabilité thermique, sont particulièrement critiques dans l'aérospatiale, où une défaillance du matériau peut avoir des conséquences catastrophiques.
Enfin, l' industrie pétrolière et gazière utilise des joints EPDM dans diverses capacités, telles que les vannes, les pompes et les systèmes hydrauliques. Bien que l'EPDM ne soit généralement pas résistant aux hydrocarbures, des applications spécialisées dans ce secteur peuvent utiliser des qualités spécifiques d'EPDM. La robustesse du matériau face aux conditions environnementales extrêmes et la facilité d'installation sont cruciales dans les environnements exigeants généralement rencontrés dans les opérations pétrolières et gazières.
EPDM durci au peroxyde ou au soufre
Lors du choix des joints EPDM, la décision clé consiste souvent à opter pour des variantes durcies au peroxyde ou au soufre . Bien que les deux types partagent les principales caractéristiques de l'EPDM, telles qu'une excellente résistance aux intempéries et une polyvalence dans toutes les applications, le processus de durcissement peut avoir un impact significatif sur leurs propriétés mécaniques et chimiques.
La création d'EPDM durci au peroxyde utilise des peroxydes organiques comme agents de durcissement, ce qui donne une structure polymère qui excelle en termes de résistance aux températures élevées et aux produits chimiques. Ce type de durcissement présente des liaisons croisées plus fortes et plus stables, contribuant à une résistance à la traction plus élevée et à une résistance supérieure à la déformation rémanente. Sa stabilité chimique accrue le rend adapté aux applications impliquant une exposition à une gamme plus large de produits chimiques telles que les industries automobile et aérospatiale.
L’EPDM durci au soufre, en revanche, utilise du soufre comme agent de durcissement, offrant ainsi ses propres avantages. Cette méthode de durcissement produit généralement des joints plus flexibles et élastiques, qualités très appréciées dans la construction et les applications à basse température. Bien qu'elle ne soit pas aussi résistante chimiquement que l'EPDM durci au peroxyde, la variante durcie au soufre fonctionne de manière fiable contre une gamme plus restreinte de produits chimiques et est généralement plus rentable.
En comparant les deux, l'EPDM durci au peroxyde excelle dans les environnements difficiles, en particulier lorsque des températures élevées ou une large résistance chimique sont requises. D'autre part, l'EPDM durci au soufre est souvent préféré pour sa flexibilité, ce qui en fait un excellent choix pour les applications dynamiques nécessitant de bonnes propriétés d'allongement. Le choix entre les deux se résume souvent aux besoins spécifiques de l'application, en équilibrant des facteurs tels que la résistance chimique, les tolérances de température et les propriétés mécaniques pour prendre une décision éclairée.
Conclusion
Les nombreux avantages des joints EPDM accentuent leur rôle indispensable dans les opérations industrielles contemporaines. Que la préoccupation primordiale soit la résistance aux produits chimiques, l’adaptabilité aux variations de température ou la durabilité environnementale, l’EPDM offre une solution à plusieurs volets qui relève ces défis avec une compétence exceptionnelle. Son adaptation omniprésente dans les secteurs justifie sa résilience et son efficacité. La comparaison entre l'EPDM durci au peroxyde et au soufre révèle en outre que cette catégorie offre des options nuancées adaptées pour répondre aux demandes spécifiques de diverses applications. Comme pour la sélection de tout matériau, une compréhension approfondie des exigences opérationnelles est essentielle pour faire un choix éclairé. Grâce à sa polyvalence, sa durabilité et sa rentabilité exceptionnelles, l'EPDM reste un candidat exemplaire pour les solutions d'étanchéité dans les conditions rigoureuses des environnements industriels modernes. Achetez des joints EPDM dès aujourd'hui en utilisant notre boutique en ligne , ou contactez-nous pour d'autres questions et demandes de renseignements.