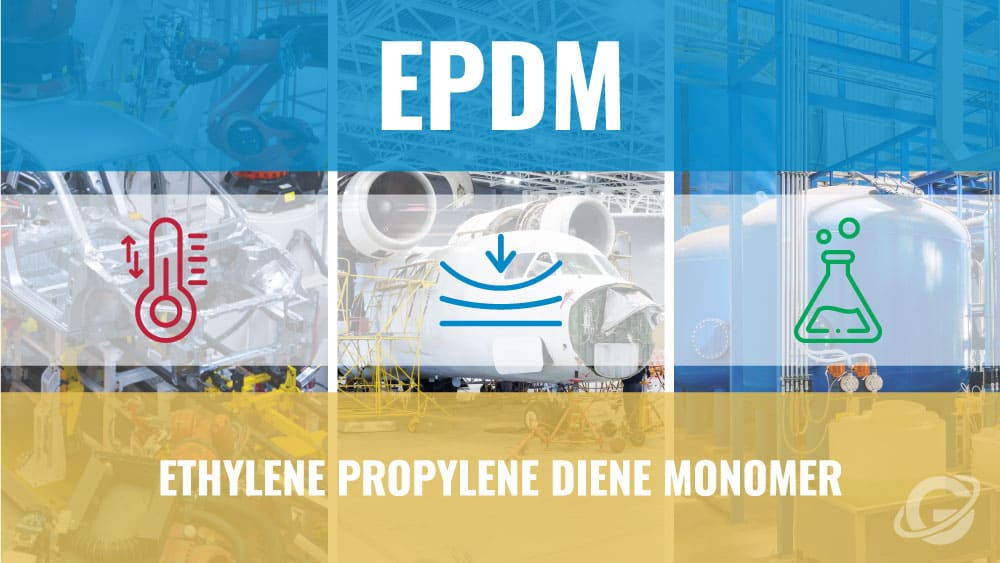
Summary
- EPDM seals are known for exceptional chemical resistance, temperature resilience, and flexibility, making them highly suitable for various industrial applications.
- Featuring cost-effectiveness, long lifespan, and minimal maintenance requirements, EPDM seals offer robust advantages in sectors like automotive, aerospace, and water treatment.
- The choice between peroxide-cured and sulfur-cured EPDM offers nuanced options for specific application needs, impacting their mechanical and chemical properties accordingly.
Introduction
The selection of appropriate sealing materials is a critical factor in optimizing performance, longevity, and safety across various industrial applications. Ethylene Propylene Diene Monomer (EPDM) has distinguished itself as a material of choice, offering an extensive array of features and advantages suitable for diverse industrial requirements. This blog comprehensively analyzes EPDM seals, elucidating their characteristic features, multifaceted benefits, and common applications. Additionally, the piece will explore variables to consider when deciding between different types of EPDM cures.
What is EPDM?
Ethylene Propylene Diene Monomer, commonly known as EPDM, is a synthetic rubber elastomer renowned for resisting several environmental conditions. Primarily made up of ethylene and propylene, derived from oil and natural gas, EPDM also contains a diene component that serves as a cross-linking agent. This unique chemical composition gives EPDM an impressive resistance to ozone, polar substances, and hot and cold water.
Developed in the 1960s, EPDM emerged as industries like automotive and aeronautics sought more robust materials to withstand challenging environments. Since then, EPDM has been a reliable option for various industrial applications, thanks to its outstanding mechanical properties. Notably, the material exhibits flexibility and durability, typically operating between -67°F to 257°F.
When you compare EPDM to other popular sealing materials like Buna (Nitrile) and Viton® (FKM), EPDM distinguishes itself with its superior water and weather resistance. Buna excels in oil-based applications, and Viton® is well-suited for high-temperature environments. Sill, EPDM is exceptionally versatile, with the capacity to resist moisture, ozone, and UV radiation effectively.
The manufacturing of EPDM seals often involves rubber injection molding. In this process, the raw EPDM material heats until it becomes malleable and then undergoes injection into a mold shaped like the desired seal. After cooling, the seal is extracted and goes through a curing process to achieve its final, application-ready properties.
Environmental sustainability is another area where EPDM shines. The material is recyclable and boasts a long lifespan, which means less frequent replacement and, consequently, less waste. Additionally, the manufacturing process for EPDM is relatively low in toxicity, further enhancing its position as an eco-friendly choice of synthetic rubber.
Features of EPDM Seals
The features of a material are paramount in determining its suitability for specific applications. Among the diverse range of sealing materials available, EPDM seals have a unique set of features that make them highly versatile and effective in various industrial settings.
EPDM is renowned for its exceptional chemical resistance against dilute acids, alkalines, and polar solvents like ketones and alcohols. This feature makes it invaluable for applications in chemical processing, wastewater treatment, and the pharmaceutical industry. EPDM’s chemical resistance is due to its saturated elastomeric backbone, which provides stability and inertness towards many reactive chemicals. The material’s resistance to a wide range of pH values, spanning dilute acids and alkalines, is attributed to its polar molecular structure that facilitates strong intermolecular forces, offering resistance against corrosive chemical attacks.
Temperature resilience is another notable quality of EPDM seals, stemming from its unique polymer architecture, which involves a diene monomer that allows cross-linking. This cross-linking contributes to the material’s high tensile strength and ability to withstand a broad range of temperatures, from cryogenic lows of -67°F to highs of 257°F. Where used in freezing climates or high-heat applications such as steam systems, EPDM retains its physical properties, minimizing the risk of seal failure due to thermal fluctuations.
Regarding flexibility and durability, EPDM owes its performance to its unique elastomeric nature and a high degree of polymer entanglement. Its amorphous structure allows for better free-volume distribution, resulting in enhanced flexibility. EPDM also exhibits a high fatigue resistance and low compression set due to its molecular architecture, which inherently resists abrasion, tearing, and impact.
EPDM stands out for its ability to withstand prolonged exposure to UV radiation, ozone, and extreme weather conditions. This characteristic derives from its saturation and the presence of protective antioxidants and UV stabilizers that prevent oxidative degradation. The material’s intrinsic resistance to UV radiation, ozone, and other oxidative agents stems from its non-polar nature, which limits the formation of free radicals that cause aging and material breakdown. This property makes it particularly useful for outdoor applications, like construction machinery or automotive weather stripping, where the seals regularly experience the element exposure.
EPDM’s dielectric constant and dielectric strength make it an excellent electrical insulator. The material has a low dissipation factor, and its non-polar structure minimizes free ion movement, rendering it resistant to electrical conductivity. This electrical insulation is particularly crucial in applications requiring stringent electrical isolation.
One of these less-discussed yet valuable attributes of EPDM is its color stability. Due to the absence of double bonds in its backbone, the material’s resistance to photo-oxidative degradation allows for color longevity and the ability to maintain its original hue. When combined with pigments or dyes, the material exhibits excellent colorfastness properties, making it ideal for aesthetically sensitive applications where color fidelity is essential.
Benefits of Using EPDM Seals
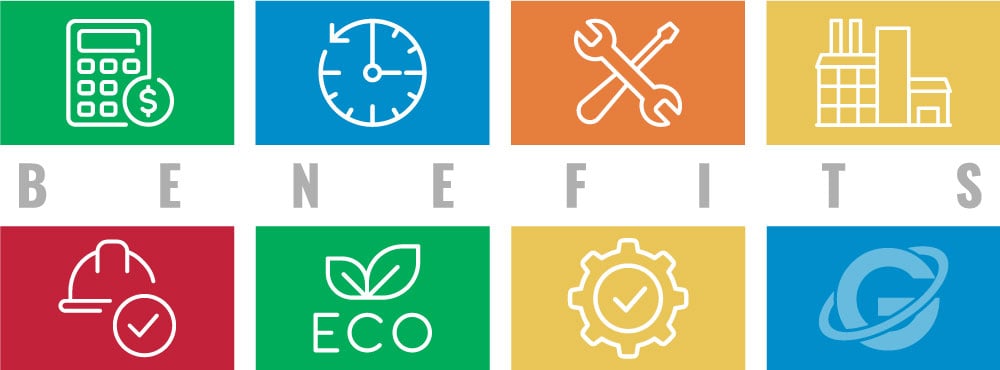
The extensive range of features offered by EPDM seals naturally translates into various benefits, making them a sought-after choice across multiple industries. Here, we delve into the key advantages that set EPDM seals apart from their counterparts.
- Cost-effectiveness: EPDM seals are often more cost-effective than other sealing materials like Viton® or Silicone when considering their lifespan and performance characteristics. Their resistance to environmental factors and a broad range of chemicals reduces the need for frequent replacements, adding to overall cost savings.
- Longevity in Applications: Thanks to their robust chemical and mechanical properties, EPDM seals exhibit a long service life. Their resistance to degradation from different external factors ensures that they remain effective over extended periods, reducing the overall cost of ownership.
- Minimal Maintenance Requirements: EPDM seals generally require less maintenance due to their durability and resistance to environmental conditions. This benefit translates into less downtime for equipment and reduced maintenance labor costs.
- Versatility Across Multiple Industries: The chemical, mechanical, and thermal properties of EPDM seals make them highly versatile. They find a wide application across sectors such as automotive, aerospace, water treatment, and pharmaceutical industries.
- Improved Safety Features: EPDM’s excellent chemical resistance and thermal stability enhance safety by minimizing the risk of seal failure that could lead to leaks or other hazardous conditions. The material’s insulating properties also make it a preferred choice in electrical applications for added safety.
- Environmental Benefits: EPDM’s long lifespan and recyclability contribute to its environmental benefits. Additionally, its production processes are relatively low in toxicity, making it a more sustainable option than other sealing materials.
- Ease of Installation: EPDM seals are easier to install than other types due to their flexibility and elastic properties. They can often be applied without specialized tools or adhesives, making the installation process quick and straightforward.
Common Applications of EPDM Seals

The automotive industry relies heavily on the durability and chemical resistance of EPDM seals. These qualities are crucial in automotive applications, such as cooling systems, brake systems, and air conditioning, where the seals gain exposure to many temperatures and potentially corrosive fluids. The longevity and minimal maintenance requirements of EPDM seals make them a preferred choice in automotive manufacturing, leading to more reliable and cost-effective vehicles.
Water treatment facilities also benefit from using EPDM seals. EPDM’s resistance to diluting acids and alkalines is a significant advantage in water and wastewater treatment applications. Here, seals gain exposure to chemicals like chlorine or other disinfectants. EPDM’s chemical resistance ensures the integrity of the seals, reducing the risk of leaks and improving overall plant safety.
In the pharmaceutical and food industries, the non-toxic and FDA-compliant nature of EPDM seals makes them ideal for use in various processing equipment. These industries often have stringent regulations around material safety and sanitation. The chemical stability of EPDM makes it suitable for applications that involve exposure to pharmaceutical formulations or food-grade chemicals. The seals’ longevity also ensures consistent performance, reducing replacement frequency and potential downtime.
Aerospace applications present unique challenges like extreme temperature fluctuations and the need for lightweight yet robust materials. EPDM seals are advantageous here due to their thermal resilience and low weight. They are common in hydraulic systems, fuel systems, and cabin sealing applications within aircraft. The improved safety features of EPDM, including chemical resistance and thermal stability, are especially critical in aerospace, where material failure can have catastrophic consequences.
Finally, the oil & gas industry employs EPDM seals in various capacities, such as valves, pumps, and hydraulic systems. Although EPDM is not generally resistant to hydrocarbons, specialized applications within this sector can use specific grades of EPDM. The material’s robustness against extreme environmental conditions and ease of installation are crucial in the demanding environments typically encountered in oil & gas operations.
Peroxide vs. Sulfur-Cured EPDM
When choosing EPDM seals, the key decision often involves opting for peroxide-cured or sulfur-cured variants. While both types share the core attributes of EPDM, such as excellent weather resistance and versatility across applications, the curing process can significantly impact their mechanical and chemical properties.
The creation of peroxide-cured EPDM uses organic peroxides as curing agents, resulting in a polymer structure that excels in high-temperature and chemical resistance. This cure type has stronger and more stable cross-links, contributing to higher tensile strength and superior compression set resistance. Its heightened chemical stability makes it suitable for applications that involve exposure to a broader range of chemicals such as automotive and aerospace industries.
Sulfur-cured EPDM, by contrast, uses sulfur as the curing agent, offering its own advantages. This curing method generally produces more flexible and elastic seals, qualities highly valued in construction and low-temperature applications. While not as chemically resistant as peroxide-cured EPDM, the sulfur-cured variant performs reliably against a narrower range of chemicals and is typically more cost-effective.
Comparing the two, peroxide-cured EPDM excels in harsh environments, particularly where high temperatures or broad chemical resistance is required. On the other hand, sulfur-cured EPDM is often preferred for its flexibility, making it an excellent choice for dynamic applications requiring good elongation properties. The choice between the two often boils down to specific application needs, balancing factors like chemical resistance, temperature tolerances, and mechanical properties to make an informed decision.
Conclusion
The comprehensive advantages of EPDM seals accentuate their indispensable role in contemporary industrial operations. Whether the paramount concern is resistance to chemicals, adaptability to temperature variations, or environmental sustainability, EPDM offers a multi-pronged solution that addresses these challenges with exceptional competence. Its ubiquitous adaption in sectors substantiates its resilience and efficacy. The comparison between peroxide-cured and sulfur-cured EPDM further reveals that his category offers nuanced options tailored to meet the specific demands of various applications. As with selecting any material, a thorough understanding of the operational requirements is essential to making an educated choice. With its exceptional versatility, durability, and cost-efficiency, EPDM remains an exemplary candidate for sealing solutions in the rigorous conditions of modern industrial environments. Shop for EPDM seals today using our online store, or contact us for further questions and inquiries.