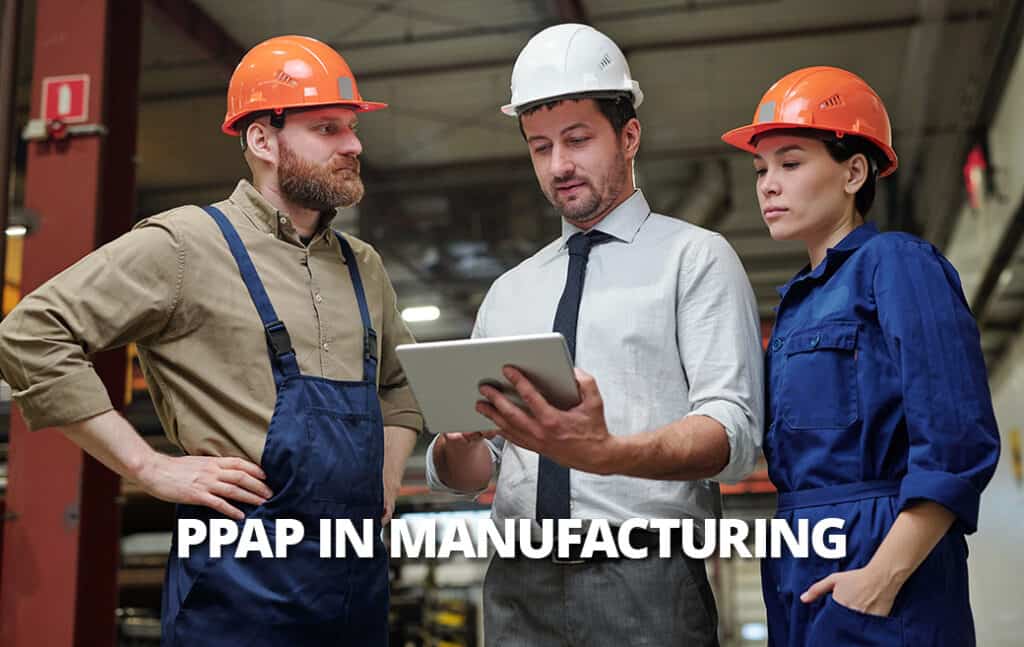
O Processo de Aprovação de Peças de Produção, ou PPAP, é amplamente utilizado na indústria de manufatura. Você provavelmente está familiarizado com o conceito se for engenheiro de projeto ou de aplicações, gerente de controle de qualidade ou profissional de MRO em uma empresa de manufatura. Esta postagem é um resumo do PPAP caso você não esteja familiarizado ou precise de uma atualização.
Como profissional de manufatura, você já sabe que os o-rings são componentes críticos em equipamentos utilizados em diversos setores. Portanto, não é surpreendente que o Processo de Aprovação de Peças de Produção também desempenhe um papel aqui.
O PPAP garante que os anéis de vedação sejam fabricados de acordo com as tolerâncias especificadas pelo cliente com um nível de capacidade de processo (Cpk) definido. Uma situação comum na fabricação é o desgaste da ferramenta, que pode comprometer a tolerância rígida exigida para anéis de vedação PPAP. Visite nossa página Visão geral dos anéis de vedação PPAP para saber mais sobre o Cpk, seu cálculo e os valores aceitáveis nas indústrias automotiva versus aeroespacial .
Uma breve história do Processo de Aprovação de Peças de Produção (PPAP)
O Processo de Aprovação de Peças de Produção, ou sua sigla PPAP, foi originalmente desenvolvido pelo Automotive Industry Action Group (AIAG) para estabelecer confiança nos fornecedores e em seus processos de produção para a cadeia de suprimentos automotiva.
“Todos os registros de projeto de engenharia do cliente e requisitos de especificação são devidamente compreendidos pelo fornecedor e que o processo tem o potencial de produzir produtos que atendam consistentemente a esses requisitos durante uma produção real na taxa de produção cotada.”
Fonte: O guia oficial do PPAP, Versão 4, março de 2006
PPAP é um subconjunto do Planejamento Avançado da Qualidade do Produto (APQP), mas não é o mesmo explicado posteriormente neste artigo.
Requisitos e a importância do PPAP
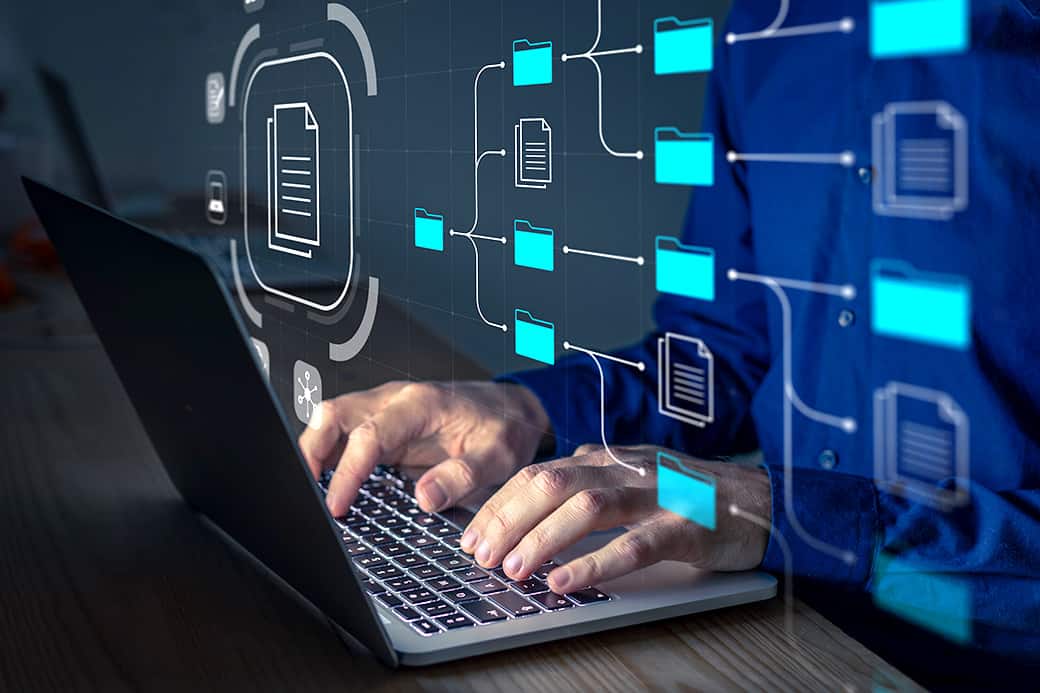
Existem 18 requisitos ou elementos para o relatório PPAP e 5 níveis de submissão.
5 níveis de submissões de PPAP:
- Nível 1: Somente envio de Garantia de Envio de Peça (PSW)
- Nível 2: PSW com amostras de produtos e dados de suporte limitados
- Nível 3: PSW com amostras de produtos e dados de suporte completos
- Nível 4: PSW e requisitos do cliente definidos pelo cliente
- Nível 5: PSW com amostras de produtos e dados de suporte completos revisados nas instalações de fabricação do fornecedor
18 elementos do relatório PPAP:
- Documentação de projeto: geralmente inclui desenhos de peças fornecidos pelo cliente junto com o pedido de compra para garantir que tudo esteja alinhado e atenda aos requisitos. Cada recurso no desenho da peça deve ser inflado ou borbulhado para corresponder aos resultados da inspeção, incluindo notas de impressão, notas de tolerância padrão e especificações.
- Aviso de alteração de engenharia: O aviso de alteração de engenharia estará presente se uma solicitação de alterações for feita em uma peça existente. O documento mostrará uma descrição detalhada da mudança em questão.
- Aprovação do cliente: Deve haver evidência de aprovação do departamento de engenharia do cliente, geralmente o teste de engenharia com amostras de peças de produção. Freqüentemente, é necessário um desvio temporário para enviar peças ao cliente antes que o PPAP seja concluído, mas os clientes podem exigir outras aprovações de engenharia como parte desta etapa.
- Análise de Modos e Efeitos de Falha de Projeto (DFMEA): A Análise de Modos e Efeitos de Falha de Projeto (DFMEA) é uma aplicação da Análise de Modos e Efeitos de Falha (FMEA) específica para o estágio de projeto. Isso permite que a equipe de design documente o que prevê sobre as possíveis falhas de um produto antes de concluir o projeto e usará essas informações para mitigar as causas de uma falha.
- Diagrama de Fluxo de Processo: O Diagrama de Fluxo de Processo mostra cada etapa da criação da peça, do início ao fim. Inclui todas as etapas principais do processamento da peça, incluindo entrada de componentes, medição e inspeção. O diagrama deve sempre corresponder ao plano de controle e à Análise de Modo e Efeitos de Falha do Processo (PFMEA). Geralmente inclui o fluxo de materiais e peças não conformes.
- Análise de Modos e Efeitos de Falha de Processo (PFMEA): A Análise de Modo e Efeitos de Falha de Processo (PFMEA) examina todas as possíveis falhas dentro do próprio processo de fabricação, avaliando cada etapa do processo de produção para indicar o que pode dar errado durante a fabricação e montagem de todas as partes.
- O Plano de Controle: O Plano de Controle lista as medidas preventivas destinadas a mitigar as possibilidades estabelecidas no PFMEA. O Plano de Controle reflete a Análise de Modos e Efeitos de Falha de Processo (PFMEA). Ele fornece maiores informações sobre como possíveis problemas podem ser verificados durante a inspeção, montagem ou inspeção da peça concluída.
- Análise do Sistema de Medição: A Análise do Sistema de Medição está em conformidade com o padrão ISO ou TS do cliente e registra todas as especificações e detalhes do equipamento que será utilizado.
- Resultados do Layout Dimensional: Os Resultados do Layout Dimensional são uma verificação de validação para garantir que as medidas no desenho estão corretas em relação ao resultado final e incluem uma lista de todas as dimensões no desenho da peça em balão e nos resultados da medição. Haverá uma lista de cada característica, especificação, resultado de medição e avaliação indicando se uma dimensão foi aprovada ou reprovada.
- Plano e Relatório de Verificação de Projeto (DVP&R): O Plano e Relatório de Verificação de Projeto (DVP&R) são registros de validação de cada teste realizado na peça, incluindo certificações relevantes do material e resultados de inspeção de aprovação ou reprovação. O cliente e o fornecedor assinarão este documento.
- Controle Estatístico de Processo ou Estudos Iniciais de Processo: Esta etapa inclui a documentação de todos os processos que ocorrerão e dos componentes que compõem o produto, incluindo gráficos SPC para características críticas. Isso demonstra que os processos críticos estão estáveis e que as construções de validação do processo podem começar.
- Documentação Laboratorial Qualificada: A Documentação Laboratorial Qualificada consiste em certificações de testes laboratoriais realizados.
- Inspeção de Remoção de Aparência (ARI): A Inspeção de Remoção de Aparência (ARI) verifica se o cliente inspecionou o produto final e indicou que todas as especificações de aparência exigidas para o design (incluindo cor, texturas, ajuste, etc.) foram atendidas.
- Amostra de peças de produção: inclui amostras da produção inicial e o local onde as peças são armazenadas é fornecido.
- Amostra Mestre: Uma amostra da versão final do produto é fornecida para ser assinada pelo cliente e fornecedor.
- Auxiliares de verificação: usados pela produção, os auxiliares de verificação são uma lista detalhada de todas as ferramentas usadas para inspecionar, testar ou medir peças durante a montagem. Os auxílios de verificação geralmente listam a peça, descrevem a ferramenta e incluem o cronograma de calibração da ferramenta.
- Requisitos Específicos do Cliente: Esta seção do PPAP é reservada para que os clientes listem suas próprias solicitações e requisitos específicos para o processo PPAP.
- Formulário de Garantia de Envio de Peças: O Formulário de Garantia de Envio de Peças resume todo o envio do PPAP, incluindo os números dos desenhos, revisões, informações das peças, números de declaração de material, desvios e resultados de testes.
NOTA: Os 18 elementos podem diferir ligeiramente entre as indústrias Automotiva e Aeroespacial.
Aqui está um gráfico útil que mostra os 18 elementos por níveis.
# | Requerimento | Nível 1 | Nível 2 | Nível 3 | Nível 4 | Nível 5 |
---|---|---|---|---|---|---|
1 | Registros de design de produto vendável | R | S | S | * | R |
1.1 | para componentes/detalhes proprietários | R | R | R | * | R |
1.2 | para todos os outros componentes/detalhes | R | S | S | * | R |
2 | Documentos de Mudança de Engenharia, se houver | R | S | S | * | R |
3 | Aprovação de engenharia do cliente, se necessário | R | R | S | * | R |
4 | Projeto FMEA | R | R | S | * | R |
5 | Diagramas de Fluxo de Processo | R | R | S | * | R |
6 | Processo FMEA | R | R | S | * | R |
7 | Plano de controle | R | R | S | * | R |
8 | Estudos de Análise de Sistemas de Medição | R | R | S | * | R |
9 | Resultados Dimensionais | R | S | S | * | R |
10 | Material, resultados de testes de desempenho | R | S | S | * | R |
11 | Estudos Iniciais do Processo | R | R | S | * | R |
12 | Documentação Laboratorial Qualificada | R | S | S | * | R |
13 | Relatório de aprovação de aparência (AAR), se aplicável | S | S | S | * | R |
14 | Produto simples | R | S | S | * | R |
15 | Amostra Mestre | R | R | R | * | R |
16 | Verificar SIDA | R | R | R | * | R |
17 | Registros de Conformidade com Requisitos Específicos do Cliente | R | R | S | * | R |
18 | Garantia de Envio de Peça (PSW) | S | S | S | S | R |
19 | Lista de verificação de requisitos de material a granel (somente para PPAP de material a granel) | S | S | S | S | R |
S = O fornecedor deverá enviar ao cliente e reter uma cópia dos registros ou itens de documentação em locais apropriados
R = A organização deve reter em locais apropriados e disponibilizar ao cliente mediante solicitação
* = O fornecedor deverá reter em locais apropriados e enviar ao cliente mediante solicitação
O processo rigoroso e o relatório documentado do PPAP garantem que as peças fabricadas pelos fornecedores atendam às expectativas de consistência e qualidade do cliente.
Os fabricantes têm a garantia da precisão e repetibilidade das peças utilizadas em sua produção. Além disso, o PPAP ajuda a reduzir o risco de defeitos aparecerem mais tarde e/ou evitar recalls dispendiosos, ao mesmo tempo que reduz o tempo de lançamento no mercado.
Tanto fornecedores quanto clientes se beneficiam com o uso do PPAP.
Adoção do processo de aprovação de peças de produção em outras indústrias
Embora seja verdade que o processo de aprovação de peças de produção foi desenvolvido para a indústria automotiva, ele agora é usado em muitos setores diferentes, como militar e aeroespacial , médico e farmacêutico e ambientes de salas limpas para os setores de semicondutores e de saúde.
Ajudamos com testes e documentação como parte do pacote total para nossos clientes. Temos em estoque uma variedade de anéis de vedação Classe VI da USP para aplicações médicas e farmacêuticas que são compatíveis com a FDA e são fabricados com materiais da lista branca para que o produto final atenda à aprovação da FDA.
PPAP x APQP
O PPAP é um componente do APQP (Planejamento Avançado da Qualidade do Produto), um processo definido utilizado para introduzir um novo produto no mercado ou para incorporar alterações em um produto após seu lançamento inicial. O PPAP é uma das 5 principais ferramentas de qualidade da norma IATF 16949:2016 para sistemas de gestão de qualidade do setor automotivo.
O APQP é executado por uma equipe multifuncional que envolve profissionais de engenharia, fabricação, garantia de qualidade e compras para atender aos requisitos do cliente.
Se os resultados do PPAP não atenderem às expectativas do cliente, é um bom sinal de que o APQP não está funcionando corretamente. O teste para ambos os processos é um teste de produção. Se o produto final de teste incluir peças defeituosas, o fabricante terá que revisar toda a cadeia de fornecimento para determinar onde as coisas deram errado.
Considerações finais sobre PPAP
O PPAP pode ser visto como uma negociação direta entre clientes e fornecedores para determinar como cada elemento do processo deve ser satisfeito. Nem todo PPAP é igual, portanto a negociação deve sempre ocorrer antes que um requisito seja aceito e o processo seja implementado. Isso garantirá que ambas as partes tenham as mesmas expectativas.
O processo PPAP pode ser altamente detalhado e demorado, mas garante que todos os elementos sejam planejados e considerados antes e durante o processo de produção para minimizar erros, reduzir desperdícios e entregar um produto de alta qualidade. Além disso, o relatório PPAP fornece aos clientes informações abrangentes para validar todas as áreas do processo de design e produção, garantindo, em última análise, que apenas produtos de alta qualidade sejam enviados ao cliente final.
Um número limitado de fornecedores pode fornecer este serviço aos seus clientes. Global O-Ring and Seal pode obter todos os níveis de documentação PPAP. Isso inclui tudo, desde compostos, corte de ferramentas, cura e controle de temperatura (em todas as cavidades do molde) no processo de moldagem por compressão. Nossa capacidade de fornecer suporte abrangente para PPAP demonstra nosso alto nível de controle sobre nossos processos de fabricação.
Ligue para 832.271.5218 para obter mais informações ou preencha o Formulário de RFQ para solicitar um orçamento.