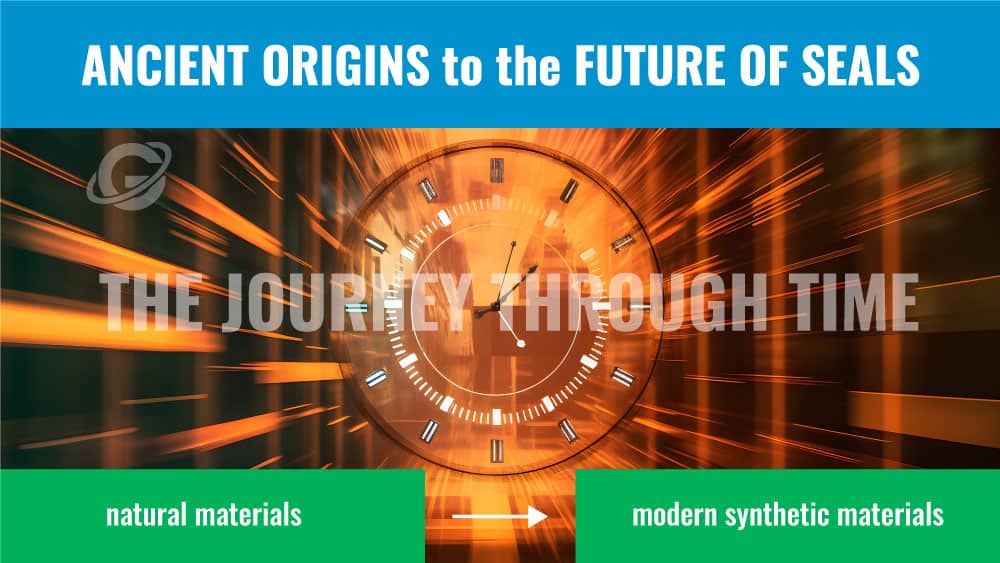
Summary
- The evolution of sealing solutions spans from ancient civilizations using natural materials to modern synthetic materials, reflecting a history of innovation driven by changing industrial needs.
- Technological advancements in seal design have enhanced sealing efficiency and versatility by developing o-rings and x-rings and integrating standard sizing.
- The future of sealing technology is moving towards intelligent, sustainable solutions with smart technology integration, predictive maintenance through IoT, and advancements in material science for diverse applications.
Introduction to Sealing Solutions
The history of sealing technology is a narrative that intertwines closely with the advancement of human civilization. From the rudimentary seals of ancient societies to the complex, intelligent sealing systems of the modern era, the evolution of these crucial components mirrors our journey of progress and innovation. Often overlooked yet essential, seals have been vital in shaping various industries, ensuring their efficiency, safety, and reliability. This exploration into the history of sealing solutions reveals a story of continual adaptation and technological breakthroughs. As we journey through time, we witness the transformation of materials and designs, reflecting each era’s changing needs and technical capabilities. This tale of evolution is not just about the seals themselves but also about the human ingenuity that has driven their development, constantly pushing the boundaries of what is possible in pursuing advancement and efficiency.
Historical Beginnings and Early Innovations

Sealing solutions are as old as civilization, with roots tracing back to ancient societies. These early chapters in the history of seals reveal a fascinating evolution from rudimentary materials to the sophisticated technologies we see today.
In ancient times, long before the advent of modern industrial seals, natural materials like clay and wax were the cornerstones of sealing technology. These materials played a primary role in securing and authenticating documents and goods. For instance, clay seals were commonly employed in Mesopotamia to secure the contents of jars and containers, ensuring they remained untouched during transport. Similarly, wax seals were a standard method for authenticating documents, a widespread practice across various cultures.
As societies evolved and machinery became more sophisticated, the need for more durable and resilient sealing solutions became apparent. This evolution led to the development of seals made from leather and hemp, which offered more outstanding durability than their ancient counterparts. Leather, known for its flexibility and strength, was commonly used in water pumps and early hydraulic systems. Hemp, on the other hand, found its use in more rudimentary applications, such as caulking for ships and packing for stationary machinery. Despite these materials’ improvements, they came with their own challenges. Leather, while durable, was prone to drying out and cracking, losing its effectiveness over time. Hemp, being fibrous, could degrade and require regular replacement. These challenges necessitated continuous innovation in sealing solutions.
The Industrial Revolution introduced rubber as a sealing material and marked a significant turning point in the evolution of sealing solutions. The discovery and subsequent development of rubber offered a solution that was more durable than leather and hemp and provided greater flexibility and resistance to various environmental factors. Rubber’s early applications were revolutionary. It quickly became a preferred material for many sealing applications due to its elastic properties, which provided an excellent seal while allowing for movement and expansion. This movement and expansion made rubber ideal for dynamic applications, something previous materials could not adequately handle.
Another significant change brought about by the Industrial Revolution was the shift from handcrafted seals to mass production. Growing demand for seals in various industrial applications drove this transition and the need for standardization in size and quality. Mass production allowed seals to be more consistent and made in larger quantities, meeting the growing needs of the rapidly industrializing world.
One of the most noteworthy applications of early rubber seals was in steam engines and early automobiles. In steam engines, seals were crucial for containing high-pressure steam and preventing leaks in joints and valves. In the burgeoning automotive industry, rubber seals were used in engines and transmissions to contain oil and prevent contamination. Despite the advantages rubber brought, it had its challenges. In steam engines, rubber seals had to withstand extreme temperatures and pressures, necessitating the development of more heat-resistant rubber compounds. In automobiles, seals were subjected to various harsh conditions, including exposure to oil and varying temperatures, leading to the development of more durable and oil-resistant rubber varieties.
The historical beginnings and early innovations in sealing solutions laid the foundation for today’s modern sealing technologies. From using natural materials in ancient civilizations to introducing rubber during the Industrial Revolution, the ever-changing needs and challenges of the times drove each step in this evolution. These early developments set the stage for continuous innovation and advancement in sealing technology, shaping the world of industry and machinery.
Development of Modern Materials
The development of modern materials in sealing solutions represents a significant leap forward from the early days of natural rubber and basic materials. Remarkable advancements in synthetic materials and the introduction of high-performance compounds characterized this period and reshaped the landscape of industrial seals.
The discovery and synthesis of synthetic materials like Buna (Nitrile), Viton (FKM), and EPDM marked a turning point in the history of sealing solutions. Nitrile, or Buna, known for its excellent resistance to oils and solvents, quickly became a staple in industries where fuel and oil resistance was crucial. Viton (FKM), with its remarkable heat resistance, proved ideal for applications involving high temperatures. With its outstanding weather and ozone resistance, EPDM became the material of choice for outdoor applications and in the automotive industry for weatherstripping and seals.
These synthetic materials offered several comparative advantages over natural rubbers. They provided enhanced resistance to a more robust range of chemicals, temperatures, and wear, making them suitable for more demanding and varied applications. Their ability to maintain flexibility and sealing properties under extreme conditions significantly improved over natural rubber, which could degrade under similar circumstances.
The impact of World War II was particularly notable in synthetic rubber development. The war created a situation of resource scarcity, particularly for natural rubber, which was a critical material for military applications. This scarcity accelerated the development of synthetic rubbers as nations sought alternatives to natural rubber for use in military vehicles, aircraft, and other equipment. Many innovations developed during this time laid the groundwork for what would become industry standards in the post-war era.
Researchers made further advancements by developing materials resistant to extreme temperatures and chemicals. They formulated new compounds to withstand harsh industrial environments, where exposure to aggressive chemicals or excessive heat and cold was common. Case studies in industries such as chemical processing, aerospace, and automotive manufacturing demonstrated the effectiveness of these materials in extending the life and reliability of seals in challenging conditions.
The development of modern materials in sealing solutions has been a journey of innovation and adaptation. These advancements have expanded the capabilities of seals and opened up new possibilities in various industrial applications. The evolution from natural to synthetic materials has enhanced the performance of seals and broadened their applicability across a diverse range of industries.
Technological Advancements in Seal Design

The technological advancements in seal design, marked by the evolution of shapes and the integration of standardized sizing, have greatly influenced the sealing solutions industry. This evolution reflects a journey towards improved performance, versatility, and global standardization.
The shift in seal shapes over the years has responded to growing industrial demands for higher efficiency and adaptability. Initially, seals were limited to basic shapes, but as manufacturing capabilities advanced, so did the complexity of seal designs. The introduction of o-rings marked a significant advancement with their simple yet effective circular shape, proving highly versatile across numerous applications. Following this, the development of x-rings brought further innovation. With a unique cross-sectional design, x-rings offered two sealing surfaces, enhancing sealing efficiency, especially in dynamic environments where they mitigated wear and extended seal life.
A pivotal aspect of the seal design evolution has been the standardization of sizing and the introduction of the AS568 standard alongside metric sizing and o-ring cord stock. The AS568 standard, which specifies dimensions for o-rings, brought about a uniform approach to seal manufacturing and selection. It created a universally recognized system, ensuring the compatibility and interchangeability of o-rings in many applications. Adding metric sizing and o-ring cord stock was a strategic response to the globalization of the industry. It acknowledged the need for diverse seal sizes to cater to a global market with varying requirements. This development allowed manufacturers and users to enjoy a broader range of sizes and customizability, ensuring precise fitting and enhanced performance of seals in diverse applications. Integrating the AS568 standard with metric sizing catered to North American and international markets, further standardizing the industry and simplifying cross-border operations.
The evolution in seal design, highlighted by developing sophisticated shapes and integrating standardization like AS568 with metric sizing and cord stock, has been crucial in advancing the sealing solutions industry. These developments have met the diverse needs of various sectors and laid the groundwork for ongoing innovation and adaptation in sealing technology.
Seals in the Digital Age and Future Trends
The seals of the digital age and future trends indicate a significant shift towards intelligent, sustainable, and highly adaptive sealing solutions. The integration of smart technologies, the focus on eco-friendly materials, and the anticipation of future technological advancements are setting the stage for a new era in sealing technology, where efficiency, sustainability, and innovation converge to meet the needs of a rapidly evolving world.
The integration of smart technology into sealing solutions is a transformative development. One of the most notable advancements is the development of sensor-equipped, intelligent seals. Embedded with sensors, these smart seals actively monitor various parameters like temperature, pressure, and wear. This real-time data collection enhances maintenance strategies and predictive capabilities, allowing for timely interventions that prevent failures and extend the seal’s life.
Predictive maintenance, powered by the Internet of Things (IoT), plays a significant role in the modern sealing industry. As integral components in machinery and industrial systems, seals are now part of the IoT ecosystem. The data collected from smart seals feeds into predictive analytics models, enabling the anticipation of potential issues before they occur. This approach extends the life and performance of seals by facilitating timely maintenance, reducing downtime, and improving overall system reliability.
The future of sealing technology is poised to be influenced by several emerging technologies. Innovation in material science, nanotechnology, and smart materials will likely bring about significant changes in seal design and functionality. Looking ahead, the sealing industry faces the challenge of keeping pace with rapidly advancing technologies and changing environmental regulations. The demand for seals operating in increasingly harsher conditions, such as extreme temperatures and corrosive environments, is expected to grow. Additionally, the industry must adapt to the evolving landscape of digitalization and IoT integration. The solutions will likely involve a combination of advanced material science, innovative design approaches, and the integration of digital technologies to create more efficient, reliable, sustainable, and intelligent seals.
Conclusion: The Continuous Evolution of Sealing Solutions
This journey of evolution, innovation, and adaptation in sealing solutions is more than just a historical overview; it’s a blueprint for the future. As we embrace the challenges and opportunities ahead, the sealing industry is well-positioned to continue its vital role in supporting and advancing global industries. From ensuring the safety and efficiency of machinery to adapting to the digital and sustainable demands of the future, the story of sealing solutions is far from over. It’s a story that will continue to unfold, driven by innovation, shaped by necessity, and guided by the vision of a more efficient, sustainable, and technologically integrated world.