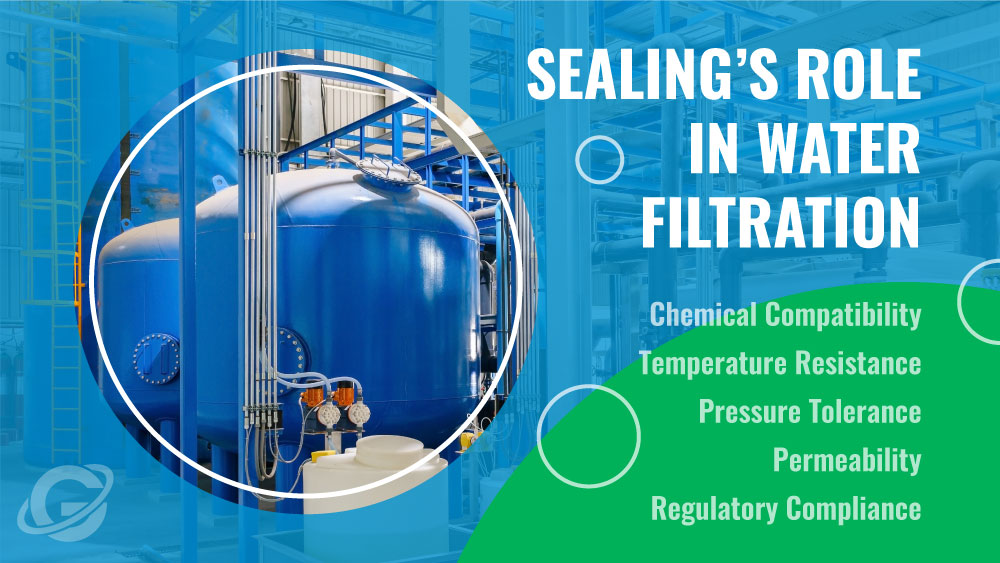
Summary
- Seals in water filtration systems are critical in ensuring operational integrity, adapting to diverse demands, and preventing contamination, directly impacting water quality and system performance.
- The evolution of seal technology in water filtration has been marked by innovation, transitioning from basic materials to advanced, sustainable solutions driven by regulatory and environmental changes.
- Material selection for seals is crucial, balancing chemical compatibility, temperature resistance, and pressure tolerance, with a focus on cost-effectiveness and compliance with global regulatory standards.
Introduction
In the intricate world of water filtration systems, the significance of seals is often understated. Yet, they play an indispensable role in ensuring these systems’ effectiveness, safety, and efficiency. Seals maintain a delicate balance of operational integrity, adaptability, and compliance within the water filtration process. This post explores seals’ multifaceted roles, their historical evolution, the challenges they’ve overcome, the regulatory landscape they navigate, and the crucial importance of material selection in their design. By understanding these aspects, we gain a deeper appreciation of how seals contribute to the functionality of water filtration systems and embody the advancements and innovations within the industry.
Role of Seals in Water Filtration Systems
The role of seals in water filtration systems is multifaceted and vital. They ensure the system’s integrity, adapt to various operational demands, resist different environmental stressors, prevent contamination, and directly influence the system’s overall performance and filtered water quality.
Seals are pivotal in maintaining the integrity of a water filtration system. They provide airtight and watertight closures, crucial for preventing leaks and maintaining the necessary pressure. This aspect of seal functionality is not just about avoiding water wastage; it’s integral to the system’s operational efficiency. Even minor leaks or pressure imbalances can lead to significant losses in system efficiency and potential failures. The ability of seals to maintain this integrity under various operational conditions keeps the filtration system running smoothly and effectively.
The adaptability of seals to different system requirements is another facet of their critical role. Water filtration units consist of diverse components like pumps, valves, and filters, each with unique sealing needs. The design and material of seals vary accordingly. For example, seals in pumps must accommodate dynamic movement and withstand high pressure, while those in static parts of the system focus on preventing fluid leakage over long periods. This versatility in design and functionality ensures that every part of the filtration system operates optimally, contributing to the overall effectiveness of the water purification process.
The ability of seals to meet varying pressure and chemical resistance requirements is essential. The operational environment of water filtration systems can involve different pressures and exposure to various chemicals. Therefore, selecting a suitable material for seals is critical. Materials like Buna, Viton, EPDM, and Silicone are chosen based on their specific benefits in pressure tolerance and chemical resistance. This careful selection prevents seal degradation over time, ensuring the longevity and reliability of the filtration system.
As often understated, the critical role of seals is in preventing contamination. Effective seals ensure that the water remains uncontaminated by external substances during the filtering, a factor crucial in maintaining water purity. This aspect is essential in applications where water quality directly impacts health or product quality, such as in drinking water systems or specific industrial applications. By preventing contaminants ingress and filtration media leakage, seals safeguard the integrity of the entire filtration process.
Finally, the impact of seals on water quality and the overall performance of the filtration system is critical. The condition of seals directly links to the filtration efficiency. Degraded or improperly fitted seals can allow impurities to pass through or cause system inefficiencies, reducing water quality. Therefore, regular inspection and timely maintenance of seals are integral to maintaining the optimal performance of the filtration system. In summary, the health of the seals is a direct indicator of the health and efficacy of the water filtration system itself.
Historical Evolution and Key Challenges in Seal Technology
The history of seal technology in water filtration is a story of innovation, adaptation, and overcoming challenges. It reflects a journey from simple beginnings to sophisticated solutions, adapting to ever-evolving demands and regulations. This evolution highlights technological advancements and underscores the seal’s vital role in water purification.
During ancient times, sealing technology used natural materials like leather and wax to prevent leakage in rudimentary water systems. However, the Industrial Revolution marked a turning point, introducing more durable materials like rubber and metal. In water filtration, the evolution of seals mirrored advancements in filtration technology, evolving from basic gaskets to complex, precision-engineered components.
Initially, manufacturers made seals from readily available natural rubber, leather, or wax materials. Though effective for simple applications, these materials had durability and chemical resistance limitations. As industrial needs grew more complex, the demand for more resilient materials led to the development of synthetic rubbers and polymers, offering enhanced properties like temperature and chemical resistance.
Significant milestones in seal technology include the introduction of synthetic elastomers, like Buna and Viton, which offered superior performance over natural rubber. The invention of Teflon (PTFE) marked another leap, providing exceptional chemical resistance. Each of these developments represented a significant step forward in the ability of seals to meet the demanding requirements of modern water filtration systems.
Throughout its evolution, seal technology faced numerous challenges. Early seals struggled with rapid wear, chemical degradation, and temperature sensitivity. Overcoming these hurdles required new materials and innovations in design and manufacturing processes. Advances like precision molding and computer-aided design (CAD) allowed for the production of seals with exacting tolerances and complex geometries suited for specific filtration applications.
The impact of broader technological advancements on seal design has been profound. Integrating computational tools and simulation software has allowed engineers to predict seal performance under various conditions, leading to more efficient and reliable designs. Additionally, advancements in material science have enabled the creation of seals that can withstand extreme conditions while maintaining their integrity.
In recent years, there has been a significant shift towards more sustainable and efficient materials in seal manufacturing. Environmental concerns and the need for longer-lasting seals drive this transition. Modern materials offer improved performance and reduce environmental impact, exemplifying the industry’s commitment to sustainability.
Regulatory standards have greatly influenced the evolution of seal technology. Regulations concerning water quality, environmental protection, and material safety have prompted the development of seals that perform effectively and comply with stringent safety and environmental guidelines. This regulatory environment has been a critical driver in advancing seal technology, ensuring it keeps pace with industrial needs and societal expectations.
Regulatory and Compliance Aspects of Filtration Seals
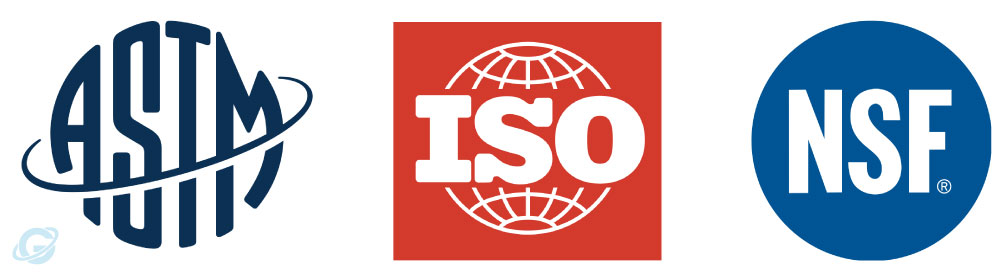
The landscape of regulatory compliance in the seal industry, particularly for water filtration systems, is both complex and dynamic. Navigating this landscape is crucial for manufacturers to ensure not only the effectiveness of their products but also their adherence to global standards.
Regulations and standards governing filtration seals vary depending on the application and geographic location. These regulations generally focus on material safety, operational efficiency, and environmental impact. Key standards include those set by organizations like the American Society for Testing and Materials (ASTM), the International Organization for Standardization (ISO), and various national health and safety bodies such as the National Sanitation Foundation’s (NSF) Standard 61. These standards ensure that seals meet essential criteria for performance and safety.
Regulatory changes can significantly impact seal design and the materials used. For instance, regulations limiting certain chemicals or mandating specific environmental performance standards drive the development of new materials and designs. Manufacturers must stay abreast of these changes to ensure their products remain compliant and competitive.
Navigating the compliance landscape becomes more complex in global markets, where regulations can vary significantly from one region to another. Manufacturers operating internationally must tailor their products to meet the specific requirements of each market, which can involve significant research, development, and testing efforts.
To ensure ongoing compliance, manufacturers often implement comprehensive quality management systems. These systems involve regular audits, continuous monitoring of regulatory updates, and training programs for staff. Proactive engagement with regulatory developments and collaboration with industry bodies are vital strategies.
Certification bodies play a crucial role in the seal industry by providing independent verification that products meet specific standards and regulations. Their certifications serve as a seal of approval, indicating compliance and quality. For manufacturers, obtaining these certifications can be essential for market access and customer trust.
Regulatory trends will likely focus increasingly on environmental sustainability, material safety, and efficiency. These trends could lead to stricter regulations, pushing manufacturers to innovate continually regarding materials and design. Staying ahead of these trends is crucial for manufacturers to remain compliant and competitive.
One of the critical challenges in seal design and manufacturing is balancing performance with compliance requirements. While adhering to regulations is non-negotiable, manufacturers must also ensure that their products meet their customers’ functional and operational needs. This balance requires a deep understanding of both regulatory landscapes and technical requirements.
Importance of Material Selection for Water Filtration Seals
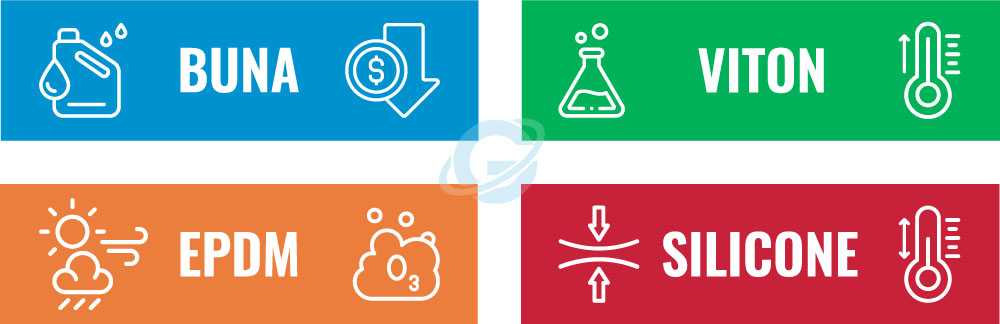
In water filtration systems, the selection of seal materials is a decision of paramount importance. The choice of material affects not only the seal’s performance and longevity but also its compatibility with specific filtration environments and compliance with industry standards.
The selection of seal materials in water filtration systems hinges on several criteria:
- Chemical Compatibility: The material must resist the chemicals it will encounter during filtration.
- Temperature Resistance: The material should withstand the operational temperature range of the system
- Pressure Tolerance: The ability of the material to maintain integrity under the system’s pressure conditions is crucial.
- Permeability: A low permeability is preferred to minimize leakage and contamination.
- Regulatory Compliance: Materials must comply with industry-specific safety and environmental regulations.
Manufacturers of seals for water filtration use various materials, each with its unique properties:
- Buna (Nitrile): Known for its excellent oil resistance, good mechanical properties, and cost-effectiveness. However, it has limited temperature resistance.
- Viton (FKM): Offers exceptional heat, oil, and chemical resistance. It’s suitable for high-temperature applications but is more expensive.
- EPDM: Excellent for hot water and steam applications, having good weather and ozone resistance. It’s not suitable for oil-based applications.
- Silicone: Known for its flexibility and temperature range, silicone is ideal for food-grade applications but has lower tensile strength.
The chemical composition and temperature of the filtered water play a critical role in material selection. For instance, high temperatures can cause some materials to degrade, while certain chemicals can lead to material swelling or brittleness. Therefore, understanding the specific environmental conditions is crucial for selecting the most appropriate seal material.
Longevity and durability are essential for ensuring the seal’s effectiveness and reducing maintenance requirements. Materials like Viton offer longer service life in harsh environments, while materials like Buna might be more cost-effective for less demanding applications. The ideal material balances durability with the specific demands of the filtration system.
Cost-effectiveness is a significant consideration. While higher-priced materials like Viton offer superior performance in demanding conditions, more economical options like Buna or EPDM might be sufficient for less aggressive environments. The decision should weigh initial costs against potential long-term savings in maintenance and replacement.
Finally, compliance with industry standards and regulations is non-negotiable. Materials must meet specifications for safety, quality, and environmental impact. This compliance ensures not only the reliability of the seal but also the safety of the water filtration process.
Conclusion
In conclusion, the journey through roles, history, regulatory challenges, and material intricacies of seals in water filtration systems illuminates their critical importance in this field. From ensuring the integrity of filtration units and adapting to diverse operational demands, navigating the complex web or global regulations, and carefully selecting materials, seals represent a fusion of engineering excellence and practical necessity. Their evolution from simple components to sophisticated, precision-engineered solutions mirrors the advancements in water filtration technology. Understanding the pivotal role of seals enhances our appreciation of water filtration technology and underscores the importance of continued innovation and compliance in this ever-evolving industry.