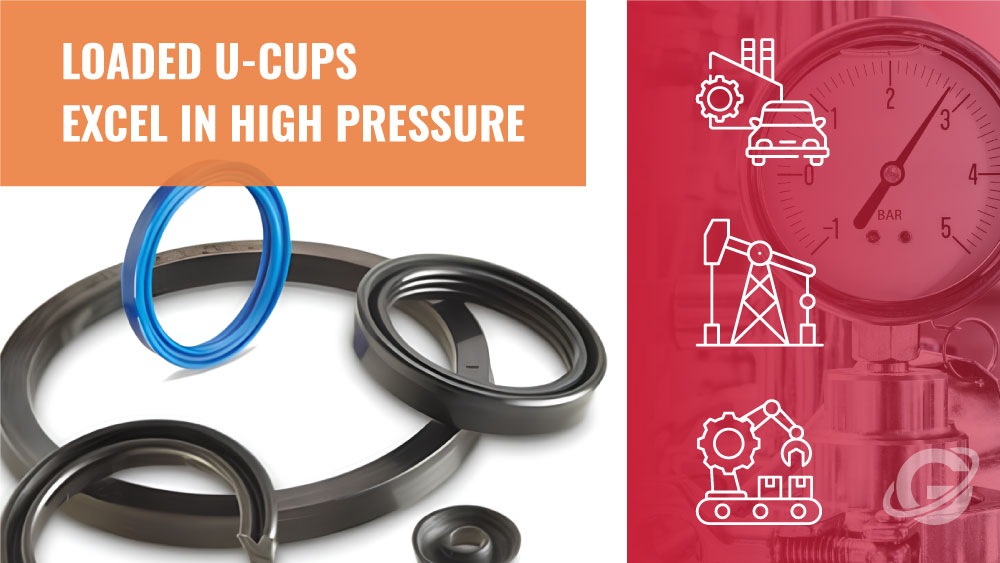
Summary
- Loaded u-cups feature a unique U-shaped profile with an energizer, excelling in high-pressure environments by providing superior sealing, durability, and adaptability.
- Their design variations cater to diverse industrial applications, from hydraulic systems to automotive manufacturing, ensuring optimal performance in dynamic and high-pressure conditions.
- Compared with piston or cord seals and v-rings, loaded u-cups offer greater versatility and longevity, making them a cost-effective choice for challenging industrial applications.
Introduction
Understanding the nuances of different seal types is vital for ensuring optimal performance and longevity in various applications. Loaded u-cups are a specialized sealing solution renowned for their robust design and exceptional adaptability, especially in high-pressure environments. This post explores the design features of loaded u-cups, their performance under high-pressure conditions, their diverse applications across industries, and a comparative analysis with other sealing solutions like piston or rod seals and v-rings.
Design of Loaded U-Cups
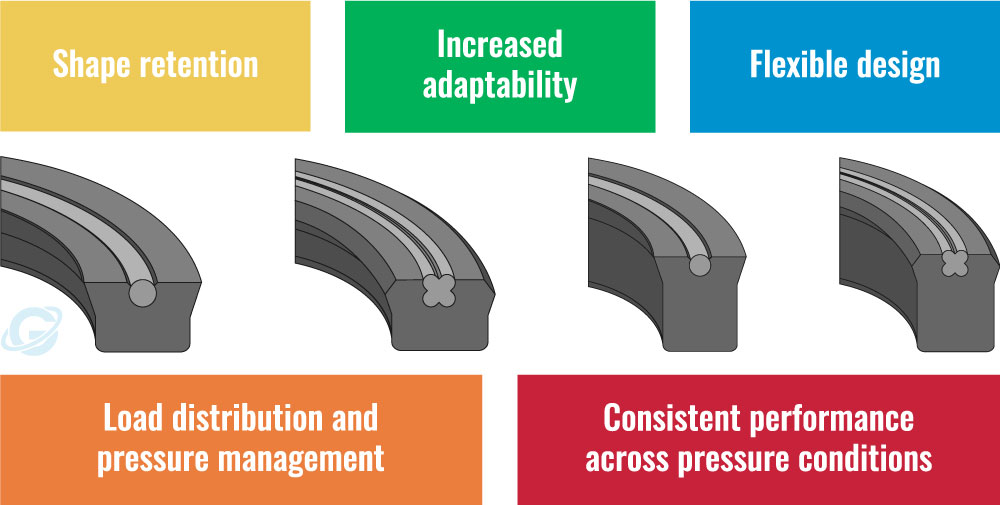
Loaded u-cups have a distinctive U-shaped profile featuring a dynamic lip for surface contact and a static lip to prevent fluid bypass. The dynamic lip’s design in loaded u-cups provides an optimal sealing force while minimizing friction and wear. Robust materials such as urethane, Nitrile, or FKM enhance the seal’s endurance. The defining feature of these seals is the energizer, either an o-ring or an x-ring, which plays a pivotal role in their functionality, significantly contributing to maintaining the sealing lips’ shape and preserving efficiency over time. Unlike standard u-cups that lack this component, loaded u-cups exhibit superior resilience and durability, particularly in high-pressure environments.
Standard u-cups are more prone to deformation and extrusion under pressure due to the absence of the energizer. With the energizer present in loaded u-cups, it ensures consistent performance and shape retention, making them ideal for demanding applications where seal integrity is critical. The energizer also improves the seal’s contact pressure against the sealing surface, ensuring consistent performance across varying pressure conditions. This feature increases the seal’s adaptability, making it suitable for multiple applications.
A crucial aspect of loaded u-cups is their ability to manage load distribution and pressure. The energizer ensures an even load across the seal’s surface, which is vital for maintaining integrity under fluctuating pressures. This even distribution minimizes point stress and wear, which is critical in high-pressure environments where seal failures can have significant implications. The design’s flexibility allows the u-cup to adapt to pressure variations, maintaining effectiveness across diverse operating conditions.
The distinction between square and deep bases is a vital design variation. A square base provides a stable foundation for applications with moderate dynamic movement. Its balanced design makes it suitable for general-purpose applications where reliability is essential. In contrast, a deep base offers a greater volume of sealing material and better absorbs pressure spikes and shocks. This design is preferable in high-pressure applications or heavy-duty operations.
The lip design, straight or beveled, also influences performance. Straight lips provide a direct sealing mechanism suitable for straightforward applications requiring simplicity and efficiency. On the other hand, beveled lips offer a progressive sealing action, reducing friction and wear in dynamic applications. This design is ideal for systems with frequent movement, where reducing friction is paramount for seal longevity.
In addition to the base and lip configurations, the type of energizer used significantly influences the performance of loaded u-cups. O-Ring energizers provide a continuous and uniform sealing force, which is beneficial in many applications, mainly where static or dynamic applications apply consistent pressure. On the other hand, x-ring energizers offer distinct advantages, particularly in dynamic applications. The X-shaped profile of these energizers provides four sealing surfaces, reducing the common issue of twisting and rolling in dynamic seals and offering improved stability. X-Ring energizers are particularly advantageous in applications with eccentric movements or misalignments. They also provide better lubrication retention, reducing friction and wear over time.
The sophisticated design of loaded u-cups, incorporating the various energizer, base, and lip options, addresses a broad spectrum of industrial sealing challenges. The selection of a particular design—square or deep base, straight or beveled lip, and o-ring or x-ring energizer—should be driven by the application’s specific requirements, considering pressure range, movement dynamics, and environmental factors. This understanding enables the optimal selection of seals, ensuring effective and durable performance in diverse industrial settings.
High-Pressure Performance
Loaded u-cups, with their distinctive design and material composition, exhibit exceptional performance under high-pressure conditions, making them invaluable in settings where seal integrity and durability are paramount. A combination of thoughtful design, strategic material selection, and innovative features like the o-ring or x-ring energizer defines their behavior and effectiveness in these environments.
When subjected to high pressure, loaded u-cups respond by expanding, but this expansion is controlled and uniform due to the energizer. This controlled expansion ensures consistent and enhanced contact with the sealing surface, which is crucial for preventing leaks even under intense pressure differentials. The design attributes, such as the deep base and beveled lip, further contribute to this high-pressure resistance. A deep base design provides additional material volume, offering a buffer against pressure spikes and aiding in resisting extrusion. Meanwhile, the beveled lip allows for a more gradual compression under pressure, which not only aids in maintaining the seal but also in adapting to varying pressure levels without compromising its integrity.
The material selection for loaded u-cups is critical to their high-pressure performance. Materials like FKM, Nitrile, and Urethane are common due to their superior tensile strength, elasticity, and resistance to deformation. These properties ensure the seals can withstand significant pressure without breaking down, maintaining their shape and sealing capabilities. This resilience is considerable in preventing equipment failure and ensuring operational safety, as the materials are less likely to suffer from wear or degradation under constant high pressure.
The benefits of such a design and material choice extend beyond coping with high pressure. Seal integrity is one of the primary advantages of loaded u-cups in such scenarios. Their ability to maintain a tight and effective barrier against fluid leaks under substantial pressure is a testament to their robust construction. This capability is crucial in high-pressure applications, as it directly impacts the reliability and safety of the entire system. Additionally, the longevity of these seals in high-pressure environments stands out. Thanks to their robust design and quality materials, loaded u-cups often have a longer lifespan than standard seals under similar conditions. This durability translates into lower maintenance costs, few replacements, and reduced downtime, critical considerations in industrial applications.
Furthermore, loaded u-cups are adept at handling pressure fluctuations, not just static high pressure. The combination of the energizer and the resilient materials allows these seals to adapt seamlessly to changes in pressure. This adaptability is essential in applications where pressure fluctuations are a norm, ensuring that the seals perform consistently over time and extend their lifespan.
The high-pressure performance of loaded u-cups is a harmonious blend of advanced design, strategic material selection, and innovative features. These elements work together to ensure that the seals can withstand the rigors of high-pressure environments, maintain their integrity, prevent leaks, and offer an extended service life. Their ability to handle static and fluctuating pressures makes them a reliable choice for various critical industrial applications.
Application Scenarios
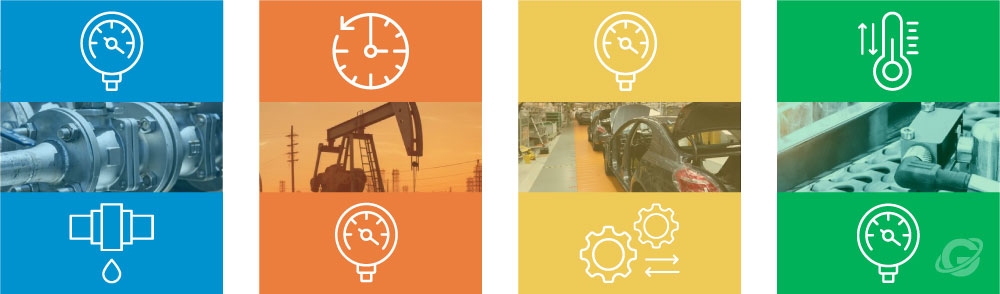
Loaded u-cups are highly valued across various industries for their robust design and exceptional performance, particularly in maintaining system integrity under challenging conditions. These seals are integral in multiple sectors, each with unique operational demands, demonstrating their versatility and effectiveness.
In hydraulic and pneumatic systems, loaded u-cups are a cornerstone, ensuring the seamless operation of machinery. Their ability to withstand high pressure and prevent fluid leaks is critical in these applications, where the integrity of the seal directly influences the system’s reliability and performance. The enhanced design of loaded u-cups, including their specialized materials and energizer mechanisms, makes them indispensable in maintaining the high standards of system integrity required in hydraulic and pneumatic applications.
The oil and gas industry, characterized by extreme pressure and harsh environments, relies heavily on loaded u-cups for their durability and pressure resistance. Utilized in equipment like drilling machinery, valves, and pumps, these seals play a pivotal role in preventing failures that could have severe consequences. The reliability of loaded u-cups in such demanding conditions underscores their importance in maintaining system integrity in the oil and gas sector.
Loaded u-cups find use in various critical systems, including brakes and transmissions, in the automotive industry. Their capability to handle dynamic movements and pressure fluctuations is essential for the smooth functioning of these systems. The automotive sector’s rigorous requirements for seals that can withstand diverse operational conditions make loaded u-cups an ideal choice, contributing significantly to the overall integrity and safety of automotive systems.
Loaded u-cups also find extensive use in the manufacturing and processing industries. The seals’ ability to reduce friction and endure wear is crucial in machinery that involves repetitive cycles and high-speed movements. Their adaptability to different operational conditions, such as temperature extremes and varying pressure levels, ensures uninterrupted and efficient manufacturing processes.
Overall, the application scenarios for loaded u-cups are diverse and demanding. Their widespread use in hydraulics and pneumatics, oil and gas, automotive, and manufacturing is a testament to their adaptability, resilience, and crucial role in maintaining system integrity. The unique advantages of loaded u-cups make them an indispensable component in various industrial and specialty applications, where their performance is essential to the success and safety of operations.
Loaded U-Cups vs Alternative Sealing Solutions
Loaded u-cups, with their specialized design featuring an energizer, demonstrate exceptional performance, particularly in high-pressure environments, outperforming piston or rod seals and v-rings in specific scenarios. This distinctive capability makes them a preferred choice in various industrial applications where reliability and durability under pressure are crucial.
Compared to piston or rod seals, which are designed primarily for hydraulic and pneumatic systems involving linear motion, loaded u-cups offer enhanced versatility. Their ability to handle high-pressure conditions and adapt to dynamic movements makes them more suitable for a broader range of applications. While piston or rod seals are influential within their specific use cases, the robust construction of loaded u-cups often translates to a longer lifespan and reduced maintenance needs. This advantage is particularly noticeable in environments with harsh operating conditions, where loaded u-cups maintain their integrity and performance over time.
Similarly, compared to v-rings, which are known for their flexibility and adaptability to wear in rotary and linear movements, loaded u-cups stand out in high-pressure scenarios. V-Rings are beneficial for their ease of installation and suitability for various applications. Still, they may not match the high-pressure resilience and long-term durability offered by loaded u-cups. The specialized design of loaded u-cups, capable of accommodating intense pressure and dynamic operational demands, renders them more effective in challenging conditions where v-rings might falter.
The cost-effectiveness of loaded u-cups becomes evident when considering their longer operational life and reduced maintenance requirements. Despite a potentially high initial investment compared to piston or rod seals and v-rings, the longevity and reliability of loaded u-cups can lead to significant savings over time, making them a more economically viable option in demanding applications.
When selecting between loaded u-cups, piston or rod seals, and v-rings, it’s essential to consider the application’s specific requirements, including the pressure range, temperature, chemical compatibility, and whether the application involves dynamic or static movements. Loaded u-cups are generally the preferred choice in more rigorous environments, where their ability to withstand high pressure and dynamic stresses is paramount.
Loaded u-cups’ performance in high-pressure and dynamic environments makes them a more suitable option than piston or rod seals and v-rings in many industrial scenarios. Their robust construction and specialized design ensure effective sealing and longevity, providing a cost-efficient and reliable solution for challenging applications. The decision to choose loaded u-cups should include a comprehensive analysis of the application’s technical demands and operational conditions.
Conclusion
Loaded u-cups stand out as a superior sealing solution in various industrial settings, mainly where high pressure and dynamic conditions are prevalent. Their unique design, incorporating an energizer and options for different bases and lip configurations, enables them to address a wide range of sealing challenges with remarkable efficiency. Choosing the correct seal type requires careful consideration of the specific application requirements, including pressure ranges, environmental factors, and technical demands. Loaded u-cups offer a blend of durability, adaptability, and cost-effectiveness, making them a compelling choice for ensuring effective and reliable sealing in demanding industrial environments.