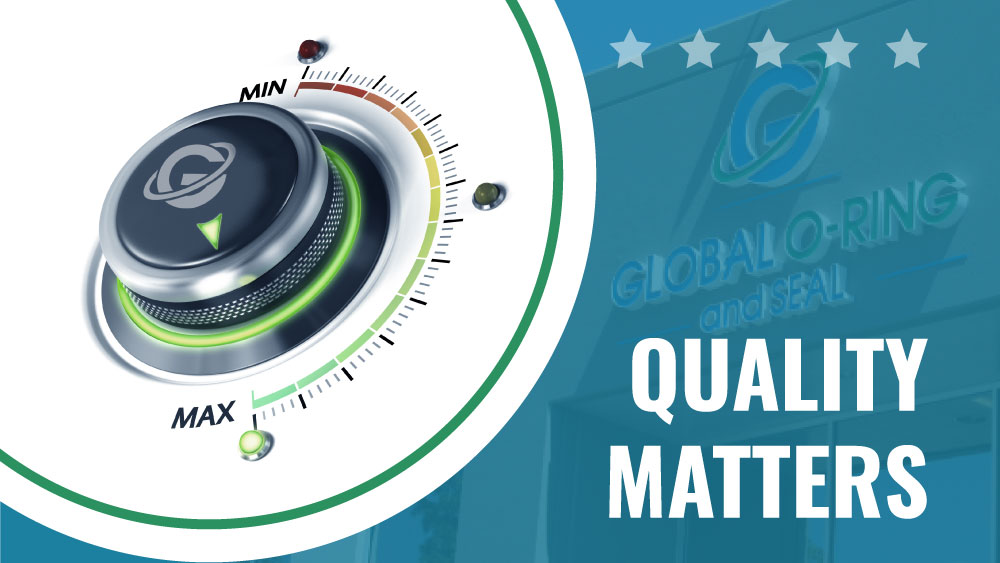
Summary
- Global O-Ring and Seal champions quality via internationally acclaimed certifications such as ISO 9001, ensuring compliance and fostering customer trust worldwide.
- Core objectives focus on consistent, on-time delivery and high-order accuracy through multi-tiered quality checks, aligning the company’s strategy with customer expectations.
- Internal and external audits strengthen Global O-Ring’s rigorous Quality Management System (QMS) while actively integrating customer feedback into ongoing quality improvements.
Introduction
In today’s increasingly competitive market, quality is the cornerstone of a thriving business. At Global O-Ring and Seal, we recognize that the pursuit of quality is not a destination but an ongoing journey woven intricately into our operational ethos. The following exposition delves into our dedication to sustaining exceptional quality, encompassing everything from internationally acclaimed certifications to our rigorous Quality Management System (QMS).
Why Quality Matters
Quality is important for several reasons, each of which highlights the indispensable role of quality in achieving business excellence and customer satisfaction. Ensuring reliability and durability, building customer trust, reducing costs, gaining a competitive advantage, and maintaining regulatory compliance are only a few reasons why quality matters.
- Ensuring Reliability and Durability: High-quality products last longer and work more efficiently, reinforcing the reliability and durability of your operations. This translates to less frequent replacements and minimal downtime, increasing overall productivity.
- Customer Trust: By consistently delivering superior products that meet and exceed expectations, we fulfill immediate needs and establish a dependable foundation for future collaborations.
- Reducing Costs: The benefits of high-quality products extend beyond immediate performance. Over time, these products lower the risk of failure, minimize maintenance costs, and save valuable time, offering our customers a significant return on investment.
- Competitive Advantage: Our high standards set us apart in the marketplace, fortifying our brand image and fostering customer loyalty. Customers recognize and appreciate the extra value that our quality products bring, making them more likely to choose us over competitors.
- Regulatory Compliance: We exemplify industry best practices by upholding rigorous quality standards. This proactive approach to compliance helps us offer our customers peace of mind knowing that our products meet the most stringent regulations for safety and performance.
Our Quality Management System (QMS)
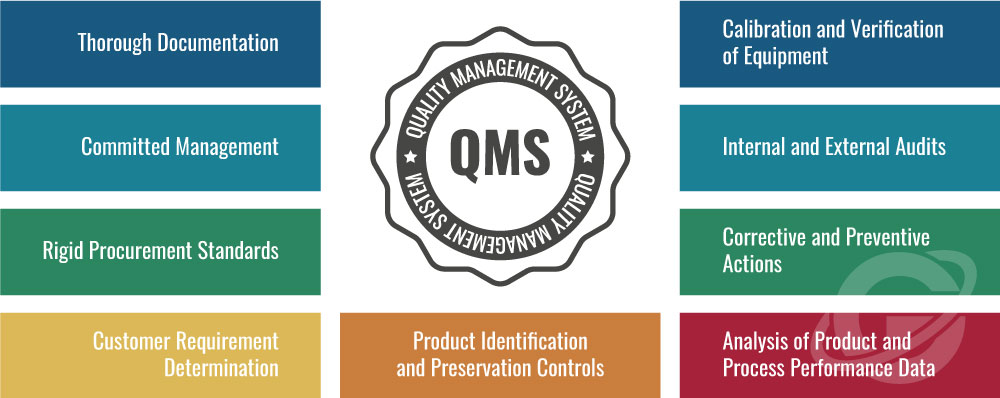
The following is a breakdown of the key components of our Quality Management System (QMS).
- Thorough Documentation and Record Retention: A well-documented process is a transparent and accountable one. Our meticulous documentation captures every detail of our operational procedures, enabling us to engage in data-driven analysis for ongoing improvement. Record retention also aids in traceability, ensuring that our performance history is accessible for audits and compliance checks.
- Committed Management and Highly Trained Personnel: Our commitment to quality extends from the executive level to every employee. Our management is deeply involved in establishing and reviewing quality objectives. Meanwhile, our staff undergo rigorous training regimens, encompassing skills development and compliance awareness, to ensure they are at the forefront of industry best practices.
- Rigid Procurement Standards: We understand that exceptional products start with superior materials. As such, we impose stringent criteria for supplier selection, including comprehensive vendor audits, verification of certifications, and quality checks on received materials, ensuring that only the best goes into our products.
- Customer Requirement Determination, Review, and Communication: We don’t just meet customer requirements; we exceed them. To do this, we continuously talk with our customers, capturing their needs and transforming them into specific product features. This process involves ongoing reviews and direct communication to ensure the final product meets customer expectations.
- Product Identification, Traceability, and Preservation Controls: Our meticulous procedures ensure every product is identified and traceable throughout its facility lifecycle. This process involves unique identification codes, careful preservation methods, and systematic monitoring, ensuring quality at every production and storage stage.
- Calibration and Verification of Measuring/Monitoring Equipment: Precise measurement is the cornerstone of quality assurance. Therefore, all our measuring and monitoring equipment undergo regular calibration and verification, ensuring the accuracy of our assessments and the quality of products that leave our facility.
- Internal and External Audits: Regular audits serve as our self-check mechanism. Whether in-house or externally, these audits review every aspect of our QMS, from documentation to process implementation. We promptly address any identified gaps, ensuring the unwavering integrity of our quality assurance.
- Corrective and Preventive Actions: Mistakes are learning opportunities. When non-conformance occurs, we swiftly identify the root causes and implement corrective actions. We also proactively examine our processes for potential pitfalls and introduce preventative measures, continually elevating our quality standards.
- Analysis of Product and Process Performance Data: Data drives decisions. We regularly scrutinize performance metrics, customer feedback, and audit results to identify areas for improvement. This analytical approach allows us to continually refine our processes, ensuring that our commitment to quality is an everyday practice.
Certifications and Compliance
ISO 9001:2015 – Quality Management System
This international standard, established by the International Organization for Standardization (ISO), sets the criteria for a quality management system. The basis of the standard covers several quality management principles, including a strong customer focus, the involvement of top management, a process approach, and ongoing improvement. Our ISO 9001:2015 certification is a doctrine that ensures we meet customer and regulatory requirements while striving for excellence. It showcases our global recognition for quality, making us a trusted supplier worldwide. It also standardizes our QMS, ensuring the same level of quality across all products and services, and it enables us to streamline our internal processes, resulting in a faster response time and more effective project execution.
IATF 16949:2016 – Automotive Quality Management System
The International Automotive Task Force (IATF) established this standard with exceptional stringency tailored to the automotive industry. Its design aims to create a quality management system fostering continuous improvement, prioritizing defect prevention, and minimizing variation and waste within the supply chain. This certification is crucial for any supplier to the automotive industry, proving the highest standards of quality, safety, and efficiency. This standard brings robustness to our QMS, focusing on defect, variation, and waste reduction in the supply chain.
ISO 45001:2018 – Occupational Health and Safety Management System
The ISO 45001:2018 standard replaces OHSAS 18001 and sets the framework for establishing, maintaining, and continually improving an occupational health and safety management system. It focuses on a proactive approach to identifying hazards and controlling risks, along with a consideration for the well-being of workers. Our manufacturer’s certification in this standard underscores the commitment to providing a safe, productive environment for employees, which, in turn, positively impacts the quality of our products. A safe environment ensures a focused and committed workforce, producing better quality products.
ISO/IEC 17025:2017 – Laboratory Testing Standard
Specific to laboratories, the ISO/IEC 17025:2017 standard outlines the general requirements for the competence, impartiality, and consistent operation of laboratories. This standard applies to all organizations performing tests or calibrations. It has elevated our manufacturer’s in-house lab’s credibility and ensures that testing methods yield reliable, consistent, and internationally recognized results, reinforcing the quality of our products.
RoHS and REACH Compliance
RoHS (Restriction of Hazardous Substances) and REACH (Registration, Evaluation, Authorisation and Restriction of Chemicals) are European standards now gaining global recognition. RoHS restricts the use of certain hazardous substances in electrical and electronic equipment, while REACH imposes obligations on manufacturers to manage the risks associated with substances. Our manufacturer’s compliance with these standards affirms our commitment to environmental responsibility and consumer safety, setting us apart as a conscientious global supplier and contributing to our overall product quality.
A Proactive Approach to Quality Assurance
Non-Conformance and Corrective Actions
While our aim is zero defects, we swiftly at if a product fails to meet our quality standards. Non-conforming products are immediately identified and isolated from the compliant products. Subsequently, we generate a thorough non-conformance report outlining the precise failure areas.
Root Cause Analysis and Preventive Measures
Beyond immediate corrective actions, we also conduct root cause analysis to understand the underlying reasons for the failure. Once identified, preventive measures are taken and rigorously validated. This approach resolves the issue at hand and serves as a preventive mechanism against similar future occurrences.
Customer Feedback for Continuous Improvement
Beyond internal procedures, we actively solicit customer feedback as another form of proactive quality assurance. This direct line to end-users offers invaluable insights into the performance of our products under real-world conditions. Each piece of feedback is meticulously analyzed and integrated into our quality assurance procedures, keeping our standards current and ahead of industry norms.
Quality Objectives
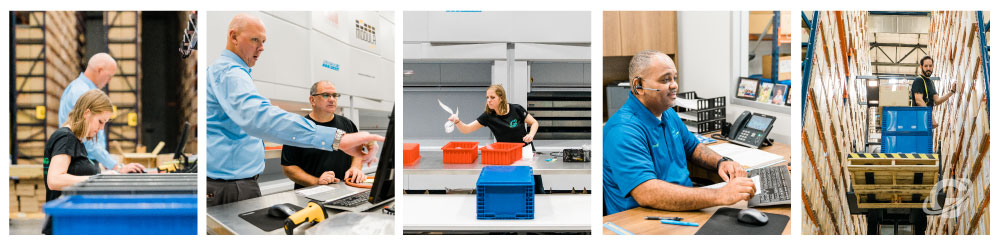
At Global O-Ring and Seal, our core quality objects serve as the backbone of our operations, influencing every decision and strategy we implement. These objects are key performance indicators that align our team and provide a measurable approach to our unwavering commitment to quality.
In a fast-paced world where delays can translate to lost opportunities, our first objective is consistent, on-time delivery. We employ cutting-edge inventory management systems coupled with real-time tracking, enabling us and our customers to monitor the progress of their orders at every stage. This ensures you receive your order as expected, without any unpleasant surprises.
Our second quality objective is to maintain high-order accuracy. We have implemented multi-tiered quality checks throughout our order fulfillment process to achieve this. These checks include order verification, picking and packing audits, and final inspections before shipping. By scrutinizing every stage, we aim to eliminate errors and achieve zero tolerance for mistakes, ensuring you receive what you ordered.
Ultimately, our quality aims to maintain exceptional customer satisfaction ratings. To ensure we meet this objective, we have established multiple channels for customer feedback and dedicated support teams trained to resolve any issues promptly and efficiently. We also regularly review this feedback as part of our continuous improvement process.
Conclusion
As we navigate an ever-competitive global market, Global O-Ring and Seal remains resolute in its foundational commitment to better quality. This commitment is not confined to a single department, but permeates the essence of our organizational structure, acting as both a driver and a benchmark for the value proposition we extend to our clients.