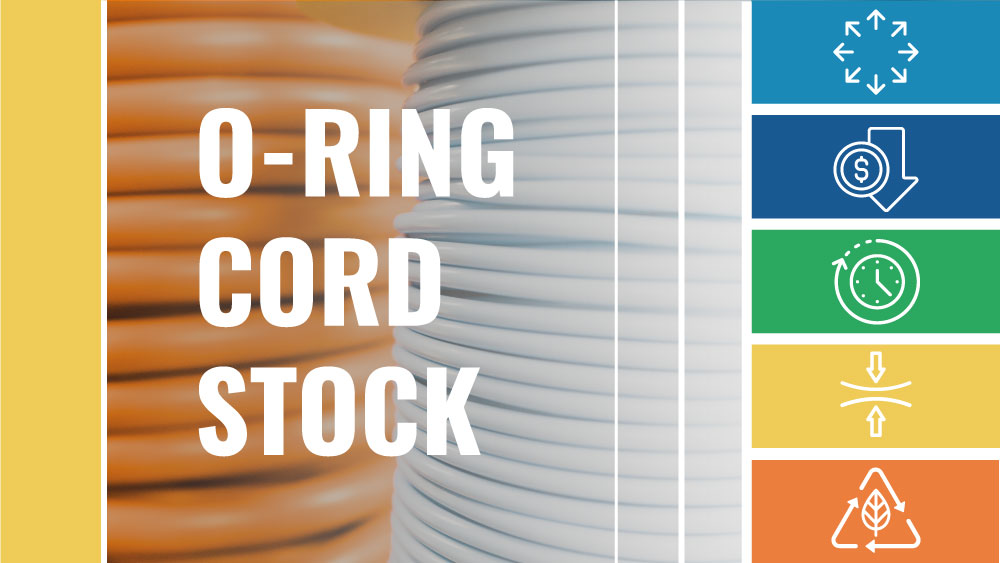
Summary
- O-Ring cord stock’s manufacturing process, from material selection to extrusion, curing, and cutting, creates a highly versatile product tailored for various applications.
- Vulcanization transforms cord into an o-ring, enhancing control, precision, and adaptation for diverse needs, making a product that meets varied application demands.
- The role of stringent quality control measures is significant, identifying and preventing common defects in cord stock production to ensure reliable performance and high standards.
Introduction
O-Rings, though small, have an omnipresent role in various applications across many industries. However, the intricacies behind them, particularly the specifics of o-ring cord stock, can seem complex and intricate. This blog post sets out to unravel the mysteries behind o-ring cord stock, taking a closer look at its unique characteristics, wide-ranging uses, significant advantages, and the pivotal role of vulcanization in its manufacturing process.
O-Ring cord stock is a diverse product meticulously manufactured from various materials to serve different use cases. It is often the preferred solution for custom needs when standard o-ring sizes do not meet the application’s specific requirements. In this exploration, we will discuss what exactly o-ring cord stock is, why it holds such a significant position in numerous industries, and how we can anticipate and prevent potential defects that might arise in the manufacturing process.
O-Ring Cord Stock: Deep Dive
O-Ring cord stock is not just a simple extruded product; it’s a marvel of modern engineering, a testament to the constant pursuit of solutions that drive the world forward. In its most basic form, it is a long, cylindrical piece of elastomer, a specialized polymer with the elastic properties of natural rubber. But it is far more than that.
The manufacturing process of o-ring cord stock is an art and science. The first step is selection of the right material. The material could be Buna (Nitrile), Viton (FKM), EPDM, Silicone, Aflas, or others, depending on the application requirements. Each of these materials has unique properties such as oil resistance, chemical resistance, high or low-temperature performance, and mechanical strength, which makes them suitable for different applications. For a full list of our cord compounds and their properties, visit our compounds page.
The selected material then goes through the extrusion process, pushing or drawing through a die of the desired cross-section. This process is a marvel of mechanical engineering, involving precise control of temperature, pressure, and speed. It demands a deep understanding of the material properties, as slight variations can significantly affect the resulting cord’s quality and performance. Furthermore, this extrusion process means that the cord often has slightly different properties than molded o-rings of the same material, such as temperature range, which is essential to consider when selecting the right solution.
The next step is to cure the continuous lengths of the cord that resulted from the extrusion process. Curing is a critical step, giving the cord its final properties. It involves heat and pressure, which causes the material to undergo a chemical reaction that strengthens it and makes it resistant to degradation. The manufacturing process concludes by cutting the cords into a range of sizes tailored to meet the customer’s specific requirements.
Advantages of Using O-Ring Cord Stock
O-Ring cord stock brings multiple advantages to the table. First and foremost is its versatility. The ability to create custom-sized o-rings from cord stock means it can provide sealing solutions for a vast range of applications, from the tiniest medical device to the largest industrial machinery.
Its cost-effectiveness is another significant advantage. Rather than manufacturing custom-molded o-rings for each unique application, which can be expensive and time-consuming, manufacturers can cut cord stock to the desired length and vulcanize it into an o-ring, saving both time and money and making cord stock a highly efficient solution for custom sealing needs.
Durability and resilience are other key benefits of o-ring cord stock. Cord’s various materials, combined with its curing process during manufacture, give it exceptional resistance to multiple conditions, including high and low temperatures, high pressures, and exposure to oils, chemicals, and other potentially damaging substances. This resilience makes it a reliable solution for even the most demanding applications.
A noteworthy advantage of o-ring cord stock is its role in reducing inventory complexity. Businesses can simplify their inventory by stocking a variety of cord stock lengths that can be cut and vulcanized into required sizes rather than holding a multitude of different-sized o-rings. This approach reduces the need for extensive storage space and simplifies inventory management.
Finally, one must uphold the environmental benefits of using o-ring cord stock. Producing only the exact size required actively and significantly reduces waste. Plus, any offcuts from the cord stock can often be recycled or reused, contributing to less material waste and supporting environmentally conscious practices. This advantage can align with a company’s sustainability goals and appeal to environmentally aware customers or industries. To read more about the cord stock offered by Global O-Ring and Seal, view our cord stock product page.
Understanding Vulcanization
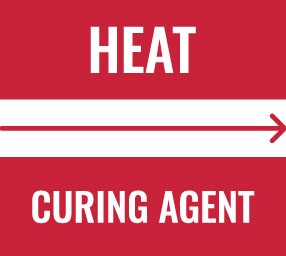
Vulcanization is an indispensable part of the o-ring cord stock manufacturing process. This chemical process, which involves treating rubber with a curing agent at high temperatures, fundamentally transforms the material, improving its strength, elasticity, and resilience.
When creating o-rings from cord stock, the cut ends fuse together through vulcanization. This process involves applying a liquid form of the uncured material to the ends and joining them together in a heated mold. The heat and pressure cause the material to cure and form a chemical bond between the ends, creating cross-links between the long-chain molecules. This results in a joint that is clean, strong, and free from defects.
Next, the vulcanized o-rings undergo inspection to ensure the joint is robust and the material is defect-free. Inspection is a critical step, as any weakness in the joint or defect in the material could compromise the o-ring’s performance. With a correctly vulcanized O-Ring, you get a product that delivers reliable performance, even in demanding conditions. To learn about our vulcanization services, visit our vulcanized o-rings product page.
Another important aspect of vulcanization is that it can significantly broaden the temperature and chemical resistance of the o-ring cord stock. The cross-linking process creates a three-dimensional network of interconnected polymer chains as the raw elastomeric material cures. This molecular structure improves the material’s durability and resistance to environmental stresses.
Additionally, the vulcanization process allows for fine-tuning the o-ring’s properties. By adjusting factors such as the vulcanization temperature and the amount of sulfur used, manufacturers can control the degree of cross-linking and, therefore, the final product’s characteristics. This flexibility allows the creation of o-rings specifically tailored to their intended application, ensuring optimal performance.
Lastly, vulcanization significantly increases the lifespan of the o-ring cord stock. Since vulcanized rubber is more resilient to wear and tear, harsh environmental conditions, and prolonged usage, it helps extend the serviceable life of the o-ring. This resilience assures performance reliability and brings about significant cost savings in the long run, reducing the need for frequent replacements. The exceptional durability attained through the vulcanization process underpins why it remains a necessary procedure in o-ring production.
The Importance of Quality Control in O-Ring Production
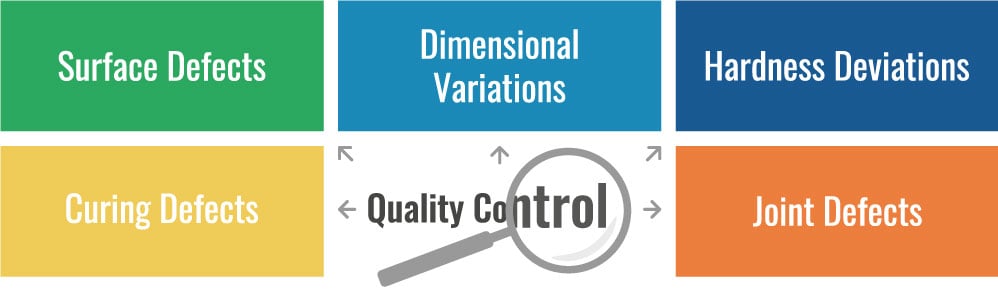
Despite its high precision, the manufacturing process of o-ring cord stock may sometimes yield defects. These faults can affect the final performance of the o-ring, potentially leading to seal failures in its applications. Here, we discuss the five most common defects encountered during cord stock production and how to prevent them.
Surface Defects: Surface defects, such as blisters or inclusions, can be caused by impurities in the raw materials or inconsistencies during extrusion. These defects may compromise the cord’s surface, affecting the seal integrity. It is crucial to ensure the quality of raw materials and the consistency of the extrusion process, including maintaining the extrusion temperature and speed to prevent surface defects.
Dimensional Variations: These variations occur when the cord’s cross-sectional dimensions (diameter) do not conform to specified tolerances. These can result from improper temperature control during the extrusion and curing processes or equipment wear. Regular monitoring and calibrating of equipment and maintaining correct process conditions can help prevent these variations.
Hardness Deviations: Cord stock that is either too hard or too soft can compromise the o-ring’s sealing ability. This deviation is often due to incorrect vulcanization conditions or formulation errors. Accurate control of the vulcanization process is necessary to avoid this, and strict adherence to the compound formula is essential.
Curing Defects: Insufficient or excessive curing during the vulcanization process can lead to a product that is either too soft and tacky or too hard and brittle, respectively. This defect is avoided by accurately controlling the vulcanization temperature and duration.
Joint Defects: When creating o-rings from cord stock, any weakness in the joint where the ends are fused can compromise the o-ring’s performance. Joint defects can result from improper application of the uncured material or insufficient heat during the vulcanization process. To prevent this, it’s essential to correctly apply the uncured material and ensure adequate heating to the joint during vulcanization.
Understanding and preventing these common defects is crucial for producing high-quality o-ring cord stock. By implementing strict control measures at each production stage, manufacturers can minimize these defects and produce cord stock that reliably meets the required standards.
Conclusion
O-Ring cord stock represents a breakthrough in engineering, bringing modern material science’s adaptability, efficiency, and resilience to the world. Its extensive application across industries underscores its importance in accelerating technological innovation and progress.
Understanding the science behind o-ring cord stock, its manufacture, vulcanization, and quality control helps us appreciate this indispensable component. Whether sealing a car engine, ensuring the safety of an aircraft, or preventing leaks in oil pipelines, o-ring cord stock is a testament to human ingenuity and the relentless pursuit of better, more efficient solutions.
In Global O-Ring and Seal’s commitment to this continuous pursuit, we offer a wide range of cord stock options to suit varied industry needs, each embodying the principles of quality and precision. Moreover, we provide in-house vulcanization services, ensuring that every o-ring we produce meets the highest performance and reliability standards.
O-Ring cord stock will undoubtedly continue to play a vital role as we continue to push the boundaries of engineering and technology. After all, sometimes the smallest components make the biggest difference. And at Global O-Ring and Seal, we are dedicated to ensuring that those small components contribute to big achievements.